【生産管理の基本】TOC理論とは?メリットや注意点、プロセスを解説
2024.11.20A0 生産管理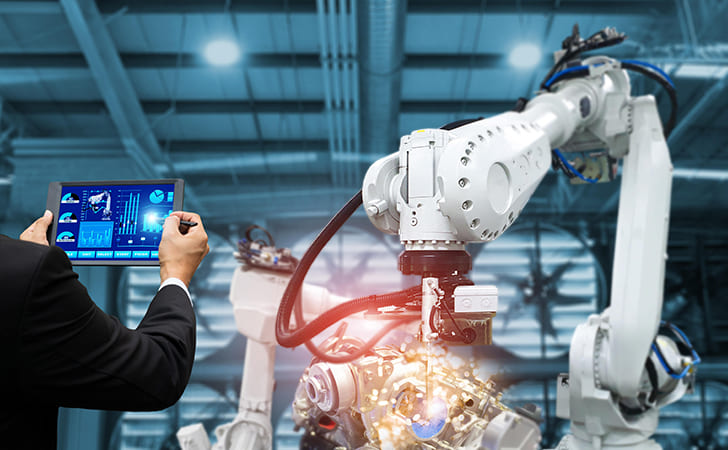
TOC理論に基づいたアプローチは、製造現場の生産性を上げる、リードタイムを半減するといった様々な効果をもたらし、売上や利益の向上に影響を与えます。製造現場のみならず、サービス業や建設業、ソフトウェア開発など、数多くの領域で成果を上げているフレームワークです。
本記事では、TOC理論の概要や基本的な考え方、生産現場にTOCを導入するメリットを分かりやすくまとめました。TOC導入時の注意点や企業が準備すべきことについても詳しく解説しています。
現場の生産性において課題を抱えている方や課題解決に向けた取り組みをお探しの方は、ぜひ参考にしてみてください。
【目次】
■TOC理論の概要
■TOC理論の基本概念
■TOC理論とトヨタ生産方式の違い
■TOC理論のメリットと注意点
■TOCを導入するために企業が準備すべきこと
■ボトルネックを素早く発見!Asprovaのススメ!
TOC理論の概要
TOC理論は「Theory Of Constraints」の略で、日本語に直訳すると「制約条件の理論」という意味合いを持ちます。製造現場の生産プロセスにおけるボトルネックの特定と改善に有効として知られている手法です。
TOC理論とは何か
システムや組織のパフォーマンスを制約する要素を特定し、その要素を改善して全体の急速な改善を目指すフレームワークです。
パフォーマンスを制約する要素、つまりゴールの達成を妨げている「ボトルネック」が、プロセスや組織のパフォーマンスを制限している、という考えに基づいています。
パフォーマンスが著しく低下している工程において、生産条件や人員、オペレーション内容に集中して改善策を打ち出すことで、効果を最大化させます。
エリヤフ・ゴールドラットの背景と貢献
TOC理論を提唱したのは、イスラエルの物理学者エリヤフ・ゴールドラット博士です。ゴールドラット博士は、「工場の生産性は、ボトルネック工程の能力以上には絶対に向上しない」という原理を提唱しました。
その原理に基づき、工場の生産性を上げるためにボトルネック工程を改善する生産を行った結果、生産性が飛躍的に高まり、工程内の仕掛りや部材在庫の減少が実証されました。
これは、ゴールドラット博士の著書『The Goal』で広く知られるようになりました。その後、工場内の改善から企業や組織全体の業績を最大にする経営革新手法として発展し、現在では工場を運営する企業のみならず、多くの組織や企業でTOC理論が採用されています。
TOC理論の基本概念
システム全体のパフォーマンスは制約条件(ボトルネック)によって決まるため、制約条件の部分を改善し続ければパフォーマンスはおのずと向上する、というのがTOC理論の基本概念です。
よって、TOCを実践するには、まずもっとも弱点となっている制約条件を特定することからはじまります。
この時に重要なのが、コストワールドとスループットワールドの見極めです。TOCではもっとも弱点となっている制約条件を特定するには、スループットを重視すべきだと考えます。
その後、「5段階集中プロセス」と「思考プロセス」の2ステップを実行し、特定した制約条件を改善していきます。
制約条件の特定
TOC理論の核心ともいえるのが、システム全体のパフォーマンスを低下させている要素(ボトルネック)を特定し、その改善に集中することです。 製造業であれば、工場で行われている工程の中で「生産効率の低下を招いているもっとも処理能力が低い工程」を特定します。生産ラインを製造プロセスごとに細かく分けて見渡すことで制約条件が見つかります。
コストワールドとスループットワールド
TOC理論では、従来の生産環境を「コストワールド」、TOCに基づく生産環境を「スループットワールド」と表現します。
TOC理論の最終目的は、コスト削減ではなくスループット(生産量やサービス提供量)の最大化です。
製造業の生産ライン全体を、1本の「鎖」にたとえてみましょう。鎖の輪の中に強度が弱いものがあると、鎖全体が弱い輪の強度と等しくなってしまいます。鎖を切れにくくするには、最も弱い輪を探して強化しなくてはなりません。
弱い輪ではなくそれ以外の輪の強度をいくら高めても、鎖全体の強度は増加しないのです。
このような考えから、TOCではコストワールドではなくスループットワールドに焦点をあてて考えます。
多くの部門で部分的な改善を行うのはコストワールドにあたり、誤った意思決定を導く可能性があると考えられています。
あくまでもスループットを重視し、コストや労力を抑えることが効果の最大化につながります。
5段階集中プロセス
制約条件を徹底的に活用するために、TOCでは以下の5段階集中プロセスという考え方を用います。
1. 制約条件を特定する
はじめに、改善すべき制約条件を特定します。生産現場においては流れが悪くなっているところを洗い出し、もっとも生産性が低下している箇所を探します。複数の要因が関わっており制約条件を特定できない場合も、1つずつ紐解いて検証していくことが大切です。
2. 制約条件を最大限に活用する
制約条件を特定できたら、その制約を解消する方法を考えます。まずは、新たな資金や人材を投入せずに改善できるかを考えましょう。現状を活かしつつ、最大限の改善ができるかを検討します。
3. 他の全てを制約条件に従わせる
制約条件だけでの問題解消が難しい時には、他の業務を制約条件に従わせる方法を用います。たとえば、制約条件の要因がある特定のプロセスの業務量過多だった場合、制約条件に合わせて業務量を減らすだけでなく、すべてのプロセスで制約条件に合わせた生産量に調整します。
4. 制約条件を改善する
ここまでのステップを実践したら、さらなる改善を目指すために設備投資や人材育成などの資金が必要な施策を実行します。制約条件の要因が作業員の能力だった場合もこの段階で対処します。社員教育やトレーニングの実施、人材の増員などによって、制約条件の改善を図りましょう。
5. 新たな制約条件を探す
TOCの効果を最大限に高めるためには、継続的な改善も大切です。ここまでのステップで制約に変化が起こったら、ステップ1に戻って新たな制約条件を特定します。
思考プロセス
TOCには、問題解決のための体系的な思考プロセスも含まれています。思考プロセスを取り入れると、複雑な問題を分解し、解決策を見つけやすくなります。
1. 問題の本質を見極める
全体のパフォーマンスに最も影響を与えている要素を見つけ出すには、生産性の低下を招いている根本原因を理解することも大切です。
生産性を低下させている問題の本質を見極めるためには、問題全体の構造や対立構造を明らかにする必要があります。現状問題構造ツリーや対立解消図をあらわすロジックツリーを用いると可視化しやすくなるでしょう。
2. 解決策を検討する
根本的な原因を見極めたら、それに対する解決策を検討するステップに入ります。
解決策を実行すると想定外の副作用が生じる可能性もあるので、本当に問題が解決するのかと同時に起こり得る副作用についても予測しなくてはなりません。
TOC理論の未来構造ツリーと呼ばれるロジックツリーを使用すると、解決策の検討と同時に副作用を予測し、予防につなげられます。
3. 実行計画を立てる
解決策を立案できたら、次に実行計画を策定します。生じる可能性のある問題や障害を洗い出し、それらを解決・回避するための行動や順序を決めておきます。解決策の実行計画を練るには「移行ツリー」、問題や障害を細かく検討するには「前提条件ツリー」というロジックツリーが役立ちます。
TOC理論とトヨタ生産方式の違い
TOC理論は、TOC理論の前身として知られる「トヨタ生産方式」と混同されがちです。トヨタ方式とはどのようなものなのでしょうか?また、TOC理論とトヨタ生産方式との違いについてもご紹介します。
「トヨタ生産方式」について
端的にいえば、トヨタ生産方式とは工場における生産活動の運用方式の1つで、生産ラインの無駄を徹底的に排除するために確立された生産方式です。トヨタ自動車の創立者である豊田喜一郎氏によって考案され大野耐一氏が開発しました。最大の敵は作りすぎのムダという考えがあり、作りすぎのムダを最も敵視しています。
トヨタ生産方式では、ムダの廃除のための2本柱「ジャストインタイム」「自働化」を掲げています。ジャストインタイムとは、必要なモノを必要な時に必要な量だけ生産することで、生産効率を高めるというものです。自働化(にんべんのついた自動化)とは、通常用いられる自動化と区別して用いられている言葉です。品質や作業に異常が発生した場合、自動で生産を止めて「人」に異常を知らせるというものです。どちらも、ムダを無くすという考えに基づいています。
TOC理論とトヨタ生産方式の違いとは
TOC理論:製造工程の中で「工程」に着目して改善を進める手法
トヨタ生産方式:製造工程の中で「働く人や労働力」に着目して改善を進める手法
TOCは作業工程に注目している点に対して、トヨタ方式では働く人や労働力に注目しているという違いがあります。TOCは、制約となっている工程を改善・強化することで収益の最大化を目指していることに対し、トヨタ生産方式ではムダを排除することで生産効率を高めるという点でも相違がみられます。
TOCは制約に集中して改善を行うことから、コストや労力を抑えながら大きな効果を得やすいのがメリットです。TOC理論とトヨタ生産方式は、どちらも製造工程のボトルネックを改善するという共通点がある一方、着目する部分に相違点があります。
TOC理論のメリットと注意点
生産現場にTOC理論を取り入れると、以下のような様々なメリットを得られますが、リスクや注意点がないわけではありません。自社や現場の状況に適した課題解決方法を選ぶためにも、メリットと注意点の両方を理解しておきましょう。
業務効率の向上
TOC理論を導入すると、ボトルネックとなる制約条件を特定し、焦点を当てて改善できるので、全体の業務効率が大幅に向上します。制約条件を特定することが作業のムダや過剰在庫の蓄積を防ぐ対策にもつながるため、全体のプロセスがスムーズになり、生産性が向上します。
問題解決能力の向上
TOC理論には、複雑な問題を解決するための体系的なアプローチ方法が含まれています。まず、現状問題構造ツリーを使って問題の根本原因を明らかにします。次に、対立解消図で複数の要因が対立する場合の解決方法を検討し、未来構造ツリーで提案した対策の効果を予測。最後に、移行ツリーを作成し、具体的な行動計画を策定します。これにより、生産管理者や経営者が迅速かつ効果的に問題に対応でき、組織全体の問題解決能力が高まるでしょう。
競争優位性の確保
TOC理論を活用することで、競合他社に対して優位に立つことができます。
生産現場は、ボトルネックの改善により業務プロセスが最適化され、リソースを効率的に利用できます。結果として、製品・サービスの品質向上やコスト削減、納期遵守など、競争力に関わりの深い要素の向上にもつながるでしょう。
特に、TOC理論のCCPM(クリティカルチェーン・プロジェクトマネジメント)を導入することで、プロジェクトの管理効率が大幅に改善されます。
注意すべき点
TOC理論を適用する際の注意点や失敗例についても考慮が必要です。
たとえば、制約条件の特定が不十分だと、期待する効果が得られないことがあります。また、改善のためのアクションが他のプロセスに悪影響を及ぼす場合もあります。TOC実践による副作用や問題の発生を予測し、予防策やプロセスに影響を与えた際の対応策を前もって決めておくことが大切です。
TOCを導入するために企業が準備すべきこと
TOC理論に基づき、企業がフレームワークに取り組む際に準備すべきことをまとめました。TOCの導入によって課題解決を図る際の参考にしてください。
制約の特定と分析
TOC(制約条件の理論)を導入する第一歩は、自社の業務フローにおける制約(ボトルネック)を特定し、この制約が全体のパフォーマンスに与える影響を分析することです。
現状のプロセスを詳細に観察し、最も遅れている部分やリソースが不足している部分を特定しましょう。
制約の最大活用と強化
制約を特定した後、その制約を最大限に活用する方針を決定し、必要に応じて強化します。
たとえば、あるプロセスの業務過多が制約になっていると判った場合には、他のプロセスも特定した制約に合わせて調整するなどの対応策が効果的です。
リソースの不足がボトルネックとなっている場合、他の部門から人員を異動させる、新たに人材を確保するなどの対応を取ります。制約となっているプロセスを効率化するにはどうすれば良いか、調整やリソースの増強によって解決を図りましょう。
方針の一貫性と従属
制約を解消するための方針を全体のプロセスに従属させ、一貫して実施します。
全ての工程や部門がこの方針に従うことで制約の影響を最小限に抑え、全体のパフォーマンスを向上させられます。
継続的な改善サイクルの確立
制約が解消された後も、新たな制約が発生する可能性があります。TOCの効果を最大化し、ゴールを達成するためには継続的な改善サイクルの確立が重要です。
常にプロセスを見直しながら新たな制約を特定し、改善する取り組みを続けましょう。サイクルを繰り返すことによって、持続的なパフォーマンス向上が期待できます。
関連する教育とトレーニング
生産管理者や経営者だけがTOCについて理解していても、現場がその方針に従えなければ効果は最大化しません。
TOCの概念や手法を社内で共有し、従業員が理解し実践できるように、教育とトレーニングを行いましょう。
特に、制約の特定と対応に関するスキルやプロジェクト管理手法(たとえばクリティカルチェーン・プロジェクトマネジメント:CCPM)についての知識を深めることが重要です。
適切なツールの導入
TOCを効果的に実施するためには、適切なツールの導入が欠かせません。たとえば、プロジェクト管理ツールやデータ分析ツール、生産スケジューラなどを導入すれば、プロセス全体におけるボトルネックや課題発見がスムーズになります。必要な人材や物資の割り当てなど、生産力向上のサポートにも有効です。
ボトルネックを素早く発見!Asprovaのススメ!
生産スケジューラ「Asprova」は、迅速かつ柔軟性の高い生産計画の立案を目指している企業様をサポートするツールです。
スケジュールの先を見据えて適切な時間配分や作業員の割り振りを行える他、設備や人員のリソースごとに分・秒単位で細かく工程を管理できます。
調達計画や配送計画、生産計画、PSI表、在庫グラフ、負荷グラフ、オーダガントチャート、資源ガントチャートなどの豊富な機能を備えており、プロセスを多角的に可視化して現場のボトルネックを発見し、業務効率化を実現します。
時代の変化や競争の激化にともない、コスト削減や生産性向上に取り組む企業が増えています。 詳しい機能や導入方法、企業での導入実績をご覧になりたい方は、こちらのページもご参考ください。

コラム編集部

最新記事 by コラム編集部 (全て見る)
- なぜこの2社は計画のブレを最小限にできたのか?精度向上のカギを解説 - 2025年7月2日
- “半日が10分に短縮”も可能に!属人化を脱し、計画作成を効率化した方法とは? - 2025年7月2日
- “なんとなく管理”からの脱却!デンカが語る、見える化による現場改善ストーリー - 2025年7月2日