【安全在庫の基礎知識】計算方法や設定するメリット・注意点を解説
2024.11.19A0 生産管理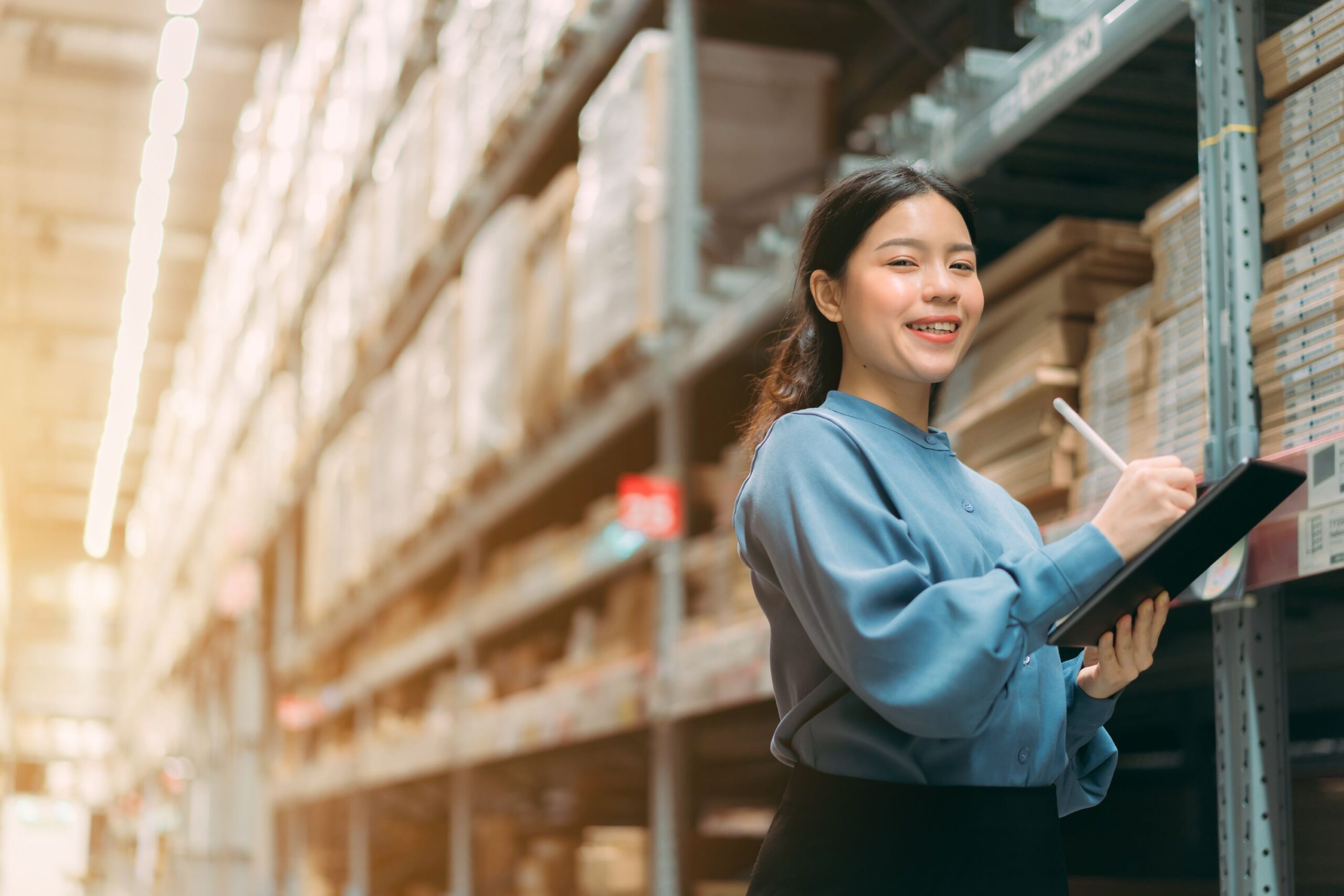
企業にとって在庫管理は、売上や顧客満足度に直結する非常に重要な課題です。その中でも特に「安全在庫」は、需要の変動や供給の遅延に対する予備在庫として機能し、在庫切れを防ぐための重要な役割を果たします。
本記事では、安全在庫の基礎知識や適正在庫の違い、計算方法や安全在庫のメリット・デメリット、設定する際の注意点など、安全在庫を理解するための幅広い知識を解説しています。効率的な在庫管理のコツや在庫管理に便利なツールについてもご紹介していますので、ぜひ参考にしてください。
【目次】
■安全在庫とは?
■安全在庫の計算方法
■安全在庫のメリットとデメリット
■安全在庫を設定する際の注意点
■効率的な在庫管理の方法
■生産スケジューラを使って安全在庫の管理を行う
安全在庫とは?
安全在庫とは、在庫切れを防ぐために必要な最低限の在庫量です。JIS規格では、安全在庫を「需要変動又は補充期間の不確実性を吸収するために必要とされる在庫」と定義付けています。
部品の需要には変動があることから、完全に欠品を防ぐことは困難です。欠品を回避するために在庫切れ前に部品を発注したとしても、供給されるタイミングが遅れると欠品が発生してしまいます。しかし、安全在庫があれば、販売予測が外れたり供給元からの納品が遅れたりした場合でも欠品を回避でき、販売機会の損失を防ぐことができます。
在庫がどのくらい必要かは市場や取引先の状況によって異なるため、これらの変動を踏まえたうえで問題ないと言える量を確保しておくのが安全在庫の考え方です。
参照: kikakurui.com:「日本工業規格JIS 生産管理用語」安全在庫と適正在庫の違いとは
安全在庫に似たような言葉に「適正在庫」がありますが、適正在庫は多すぎず少なすぎない妥当な数の在庫を確保することです。その最適な在庫量には、安全在庫も含まれています。
「欠品を防ぐための最低限の在庫量」を指す安全在庫は主にリスク管理に焦点を当てているのに対し、適正在庫は過剰在庫や欠品を防ぎ、バランスを取ることを目的としています。
安全在庫は適正在庫の要素のひとつ
安全在庫は欠品を防ぐことを目的にしているため、在庫の下限を決めるのが一般的です。上限の設定がないため、場合によっては過剰在庫が発生する可能性もゼロではありません。
一方、適正在庫では、企業や生産現場にとって適切な在庫量を確保するために上限と下限の両方を設定する必要があります。
このことから、安全在庫は適正在庫の下限を設定するひとつの要素であると分かります。
安全在庫と適正在庫の違いをしっかりと理解して適切な管理を行えるようになると、在庫切れと過剰在庫の両方を防ぎ、キャッシュフローの改善や顧客満足度の向上につながります。
安全在庫の計算方法
安全在庫を計算するにはいくつかの方法がありますが、一般的な計算式は次の通りです。
定量発注方式
定量発注方式とは、在庫の需要の変化にかかわらずあらかじめ決めておいた量まで在庫が減少した時に発注を行う方式で、発注点方式とも呼ばれます。定量発注安全在庫は、以下の式で計算されます。
安全在庫 = (1日あたりの平均使用量 × リードタイム) + バッファストック
1日あたりの平均使用量とは、過去の使用データを基に算出される1日の平均的な在庫消費量です。リードタイムは、発注してから部品が納品されるまでの日数を指し、バッファストックは、需要の急増や供給の遅延に備えるための追加在庫となります。
定期発注方式
定期発注方式とは、あらかじめ発注する期間を決めておき、スケジュールに合わせて必要量を発注する方法です。毎月に一度や3ヶ月に一度など、一定期間ごとに発注を行なって需要の変動に対応します。
定期発注方式で安全在庫を計算する際には、以下の計算式を用います。
安全在庫 = 最大需要 × リードタイム – 平均需要 × リードタイム
ここで言う最大需要とは、特定の期間における最大の在庫消費量を意味しています。平均需要は、その期間における平均的な消費量です。
定期発注方式では発注のタイミングは固定されるものの、発注量を変えることで在庫をコントロールし、過剰在庫が発生するリスクを減らせます。
ただし、適正な在庫量を決めるには、市場の景況感や取引先の状況などを踏まえて正確な需要量を予測しなくてはなりません。
過去の実績データなどを分析して毎回の発注量を決定するのが一般的です。
より高度な計算方法
さらに高度な計算方法として、需要数の標準偏差を利用する方法があります。標準偏差は平均値からのばらつきを示し、これを用いることでより精度の高い安全在庫を設定できます。この計算はExcelの関数「NORMSINV」を用いれば安全在庫係数への置き換えが可能です。具体的には、次のように計算されます。
安全在庫 = NORMSINV(1-欠品許容率) × 需要の標準偏差 × √(リードタイム + 発注間隔)
この方法では、需要の変動を正確に反映するため、過去のデータを用いて在庫使用量の標準偏差を計算し、需要の標準偏差を求めます。標準偏差に基づけば、より高度な安全在庫を算出することが可能です。
安全在庫の計算は、管理する部材の種類が少ない場合であれば人の手による算出も可能ですが、数百、数千にわたる部材の在庫計画が必要な現場の場合、人力での管理には限界があるでしょう。迅速かつ正確な在庫把握と管理体制を求めるのであれば、在庫管理を自動化できるツールを用いて計算するのがおすすめです。
安全在庫のメリットとデメリット
安全在庫を確保しておくと、生産現場は様々な状況にも柔軟に対応できるようになりますが、リスクがない訳ではありません。メリット・デメリットの両方を理解したうえで、適正な在庫管理の在り方を考えていきましょう。
安全在庫のメリット
安全在庫の主なメリットは、在庫切れや余剰在庫を回避し、生産がストップするリスクを削減して安定した事業運営につながる点です。期待できる具体的な効果は以下の通りです。
在庫切れ防止
安全在庫は、需要の急増や供給遅延に対するクッションとして機能し、在庫切れを防ぎます。製品が欠品すると、顧客への販売機会が失われるため売上や利益は落ちてしまうでしょう。予定通りの納品を期待していた顧客を裏切ることになるため、顧客満足度の低下や信頼の損失につながります。在庫切れを回避することで売上や利益、顧客満足度を維持できるようになります。
顧客満足度向上
常に製品を提供できる状態を保つことで、顧客の信頼を得ることができます。安全在庫があれば、トレンドなどが要因で市場のニーズが急激に高まり、需要が予測よりも上回った場合でも、迅速に対応できるようになります。特に、ECサイトなど流行が反映されやすい市場においては、期待された顧客体験の提供によって満足度が向上しやすくなります。
安定した事業運営
安全在庫があれば、供給チェーンの安定性が高まり、生産ラインの中断や販売の遅延を防ぎます。それにより企業の運営がスムーズになり、事業の信頼性が高まるでしょう。新規取引や契約につながる可能性があるほか、既存の取引先からの信頼度も増すことで売上や利益が向上します。
リスク管理の強化
予測困難な需要の変動やサプライチェーンの問題に対する備えが強化され、企業のリスク管理が向上します。市場変動への柔軟性が高まることによって、市場における競争力の維持・向上にもつながります。
安全在庫のデメリット
安全在庫を確保すると、メリットを得られる反面、運営には様々なリスクが生じます。安全在庫の具体的なデメリットは次の通りです。
保管コストが増加する
急な在庫切れに備えて製品の在庫を抱えるわけですから、その分の保管スペースや保管費用が増加します。発注数を誤ると過剰在庫のリスクもあり、その過剰在庫にも当然保管コストが発生します。これらのコストは企業の財務状況に影響を及ぼす可能性もあるため、いかに適正な安全在庫数を設定できるかが重要です。
キャッシュフローの悪化
リスク回避のための在庫に資金が固定されるため、他の用途に資金を回すことが難しくなる可能性があります。資金の流動性が低下し、新たな投資や緊急時の資金調達が困難になるリスクがあるのも懸念点です。
在庫の陳腐化リスク
在庫を長期間保管することで製品の価値が下がるリスクが増加します。特に、技術革新の登場が早い業界や市場のトレンドに左右されやすい季節製品などでは在庫が陳腐化し、売れ残りや廃棄リスクが高まります。
管理の複雑化
需要予測や供給チェーンの管理が必要となり、在庫管理が複雑化します。特に数百・数千もの部材を抱える事業や業態の場合、限られた人材での管理は難しいでしょう。ある程度の自動化を進めないと、安全在庫だけでなく在庫管理そのものが難しくなります。事業規模を拡大する予定でビジネスを進めているのであれば、適切なシステムやツールを導入するのがおすすめです。
安全在庫を設定する際の注意点
ここでは、安全在庫を設定する際に注意すべきポイントをまとめました。
生産現場のリスク回避のために安全在庫の設定を検討している方は、事前にチェックしておいてください。
需要の正確な予測
適切な安全在庫を設定するには、需要の変動を正確に予測することが鍵です。過去の販売データや市場のトレンドを分析し、精度の高い需要予測を行う必要があります。
正確な数値を求めるためには、計算に用いる使用量の平均値も正確に計算することも重要です。
供給リードタイムの把握
供給元から部品が到着するまでのリードタイムを正確に把握することが重要です。リードタイムが長い場合は、安全在庫を多めに設定する必要があります。また、リードタイムは、需要や時期、部材によって変動することもあります。在庫数だけでなく市場のことも考慮したうえで把握しましょう。
バッファの設定
バッファストックは、予測が難しい需要の急増や供給の遅延に備えるための追加在庫です。バッファを設定しておいて在庫量をコントロールすると、需要の変動に対応してバッファが変化し、季節変動やトレンドなどで需要が増減した際にも柔軟に対応できるようになります。バッファの設定は、リスク許容度に基づいて行います。
効率的な在庫管理の方法
安全在庫について理解できたら、業務を効率化するための方法も知っておきましょう。安全在庫管理の効率化が在庫管理業務全体を効率化し、運営全体の最適化につながります。
データ分析と需要予測の活用
過去の販売データや市場のトレンドを分析することで、需要予測を行い、より正確な安全在庫を設定できるようになります。在庫切れや過剰在庫のリスクを最小限に抑えることができますし、在庫管理が効率化し、経済的なロスを減少させることができます。
自動化ツールの導入
在庫管理の効率化には、自動化ツールの導入が有効です。これらのツールはリアルタイムで在庫状況を監視し、適切なタイミングで発注を行う機能が搭載されています。自動化ツールを使用することで在庫の過不足を防ぎ、適切な在庫量を維持できるでしょう。また、在庫管理と同時にデータ収集や分析も行えるので、今後の需要予測や分析業務の効率化も可能です。
生産スケジューラの導入
生産スケジューラの導入も在庫管理の効率化に有効な手段です。Asprova(アスプローバ)は、生産計画の最適化と属人化の解消を目的とした生産スケジューラです。
安全在庫を考慮した生産計画を立てることで、在庫不足を回避しつつ、在庫コストの削減に貢献します。
生産スケジューラを使って安全在庫を考慮した生産計画を立てましょう
アスプローバが提供する生産スケジューラを活用することで、過剰在庫となることなく安全在庫を考慮した生産計画を立てることができます。以下は具体的な活用方法の一例です。
安全在庫と生産スケジューラの連携
生産スケジューラとその他の在庫管理システムを連携させると、需要変動に迅速に対応した在庫管理ができるようになるほか、コスト削減や生産性アップなどの効果を期待できます。
在庫コストを削減
生産スケジューラは、必要な時に必要な量を生産する計画を立てることで、過剰在庫を防ぎます。これにより、安全在庫を最適なレベルに維持しながら、在庫コストの削減を実現します。
生産効率を向上
生産スケジューラを用いて計画的に生産することで、資源の確保と稼働率の向上に繋がります。これにより、安全在庫を維持しつつ、生産効率を向上させることができます。計画業務の効率化によって、担当者の作業負担も軽減されます。
生産現場における様々な業務課題を改善できる生産スケジューラは、多くの企業での導入実績を持っています。 生産スケジューラ導入によって具体的にどのような業務改善が実現したのかは、こちらのページをご確認ください。

コラム編集部

最新記事 by コラム編集部 (全て見る)
- なぜこの2社は計画のブレを最小限にできたのか?精度向上のカギを解説 - 2025年7月2日
- “半日が10分に短縮”も可能に!属人化を脱し、計画作成を効率化した方法とは? - 2025年7月2日
- “なんとなく管理”からの脱却!デンカが語る、見える化による現場改善ストーリー - 2025年7月2日