生産ライン最適化 「ラインバランシング」とは
2021.02.05A0 生産管理 , A1:生産計画・スケジューリング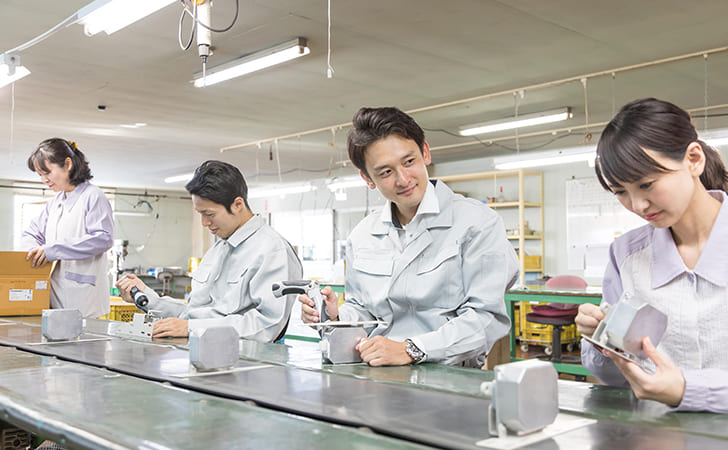
工場の生産ラインの現場において、最適化を図る方法のひとつに「ラインバランシング」という手段があります。
製造業に携わる方なら耳にしたことがあるかもしれませんが、中には「正直何をすれば良いかよくわからない」、「どんな効果が得られるのかピンとこない」という方もいるのではないでしょうか。
今回は、ラインバランシングの基礎知識を振り返りながら、ラインバランシングを行うメリットや、取り組む目的についてまとめています。併せて、ラインバランス分析の手順についてもわかりやすくご紹介します。
【目次】
■ラインバランシングとは
・工場の作業ライン能力のバランスを整える理由
・工場全体の最適化を促す手法である
・成果はピッチダイアグラムで評価する
■ラインバランシングを行う目的
■ラインバランシングのメリット
・柔軟性を保ちにくい
・ライン構造上の制約がある
・仕事が単調になりやすい
■ラインバランス分析を行う手順
・作業時間の測定
・ピッチタイムと目標サイクルタイムの計算
・問題点の発見・改善
■おわりに
ラインバランシングとは
日本産業規格(JIS)よると、ラインバランシングは「生産ラインの各作業ステーションに割り付ける作業量を均等化する方法」と定義されています。つまり、それぞれの工程の作業配分を適切にし、各作業時間がほぼ均一になるよう調整することを指しています。ラインバランシングはライン生産方式において生産効率を上げるための取り組みなのです。
工場全体の最適化を促す
ラインバランシングを行うと、生産ラインのみならず工場の生産管理全体を最適化できるようになります。そのため、組織やシステム全体の効率化を目指す際に取り組まれます。
作業の部分最適化では、一連の作業の一部を簡素化できないか、順序変更によって効率が良くならないかなど、個々の作業や設備を基準にして考えるのが基本です。それに対し全体最適化は、工場の設備や人員を最適に配置して、工場全体の効率化ができないかを考えていきます。
成果はピッチダイアグラムで評価する
ラインバランスの効率が良いかどうかは、ピッチダイアグラムと呼ばれる表を作って確認していきます。ピッチダイアグラムとは、横軸に作業ステーション、縦軸にそれぞれの作業時間を示し、時間差がどのくらいあるかを可視化するグラフです。
・ラインバランス効率=各作業者の所要時間の合計÷(ピッチタイム×工程の数) |
一般的にラインバランス効率が85%以上あると、成果が出ていると見なされます。
ラインバランシングを行う目的
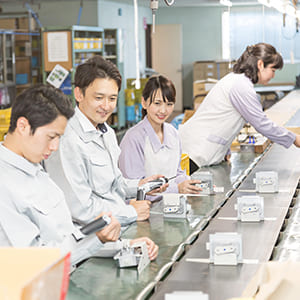
ラインバランシングを行う目的は、ラインバランス効率を改善することで生産ライン全体の効率化・最適化を図ることができるからです。
ラインバランス効率の低い生産ラインは、各作業ステーションに無駄が多いということになります。
ラインバランシングでは、各工程の「作業ステーション」を担当する作業者の作業時間やピッチタイムからデータを分析し、効率を評価して、ラインバランスを整えていきます。ピッチタイムはタクトタイムとも呼ばれます。
例えば、工程1の作業時間が長く、工程2の作業時間が短い場合、工程間に「手待ち時間」が発生し、生産効率が低下してしまいます。
そうなると、「仕掛け在庫」増加の原因にもなります。
2つの工程の作業量や人員などを見直し、工程1と工程2の作業時間を均等にできれば、仕掛け在庫の増加を防ぎ、手待ち時間の削減につながるのです。
ラインバランシングによって作業を効率化できれば生産効率が上がり、結果的に収益アップにもつながります。
ラインバランシングのメリット
ここからはラインバランシングに取り組むメリットを3点紹介します。
各項目について課題を感じている場合は、ラインバランシングを実施してみるとよいでしょう。
リードタイムの短縮
ラインバランシングによる業務効率化は、すなわち生産リードタイムの短縮です。これまでリードタイムが2日かかっていた作業をリードタイム1日に短縮できれば、短納期対応や増産依頼など、顧客のさまざまな要望に応えられるようになります。
生産性・品質の向上
ラインバランシングを行うと、工程の流れがシンプルで容易になるため、生産性も向上し品質管理が徹底しやすくなります。また、ロスタイムの解消により品質チェック等に時間を回すことも可能です。結果、製品の品質向上につながるでしょう。品質を検査する装置を導入すれば、より品質の向上と業務の効率化が見込めます。
労務費率の削減・働き方改革の推進
労働時間を短縮できれば、当然労務にかかるコストも削減できるようになります。手待ち時間が短くなれば人員カットにもつながりますし、カットできた分の人員を他の業務へ配置するなど、必要な業務に人的リソースを割けるようになります。また、労働時間の短縮により、作業現場の人員のライフワークバランスが整えば、従業員の満足度も高まるでしょう。
多品目を製造するラインや製品量や製品仕様の変更が多い工場など、ラインバランシングがしにくい現場も生産スケジューラによって生産管理全体の課題を解決できるようになります。
製造現場でよくある、「ノウハウが特定の社員に集約して属人化している」、「生産工程が複雑で前後工程のつながりがわかりにくい」などのお悩みを解決できるのが生産スケジューラです。
ライン生産方式の多くの現場で生産性向上を実現しており、多数の導入実績と蓄積されたノウハウがシステムに反映されています。
国内最大級の導入実績をもつアスプローバの生産スケジューラについて詳しく知りたいという方はこちらを参照ください。
ラインバランス分析を行う手順
ラインバランシングの基礎や必要性がわかったところで、実際にラインバランス分析を行ってみましょう。大まかな流れは以下のようになります。
- 分析に必要な数値を準備する
- ピッチタイムと目標サイクルタイムの計算
- ピッチダイアグラムの作成
- 問題点の発見・改善
ここからは、ラインバランス分析の手順を、分析のポイントや留意点も含めて解説していますので、ぜひ実践の参考にしてみてください。
分析に必要な数値を準備する
ラインバランス分析を行うには、ラインの稼働時間、必要生産量数、そして良品率が必要です。
まずラインの稼働時間を求めるには、就業時間と不稼働時間を測定しなければなりません。
工程単位や作業者ごとに分けて、それぞれの時間を測定します。なるべく多くの手待ち時間を発見するためにも、各作業ステーションの作業を細かく分けることがポイントです。計算式は以下の通りです。
・ライン稼働時間=就業時間―不稼働時間 |
次に必要生産量数です。これは需要予測を行い、今後の平均月間生産量を値として採用します。
そして良品率ですが、これは以下の式から算出できます。
・良品率(%) = 良品数 ÷ 完成品数 × 100 |
もし職場で記録したものがあれば、それを使うのがおすすめです。工程単位や作業者ごとに分けて、それぞれの作業時間を測定します。なるべく多くの手待ち時間を発見するためにも、各作業ステーションの作業を細かく分けることがポイントです。
作業時間の測定が完了したら、各工程の作業時間を可視化するピッチダイアグラムを作成します。
ピッチタイムと目標サイクルタイムの計算
ピッチタイム |
作業を開始した後、製品がラインから送り出されていくまでの時間間隔のこと。 |
目標サイクルタイム |
必要生産量を稼働時間内で製造するために必要な時間間隔のこと。 |
ピッチタイムとは、作業を開始した後、製品がラインから送り出されていくまでの時間間隔を指します。ラインバランス分析では最長時間を把握するため、工程の最大値をピッチタイムとします。
次に、目標サイクルタイムを求めます。目標サイクルタイムとは、必要生産量を稼働時間内で製造するために必要な時間間隔です。これは、最低限この時間間隔で生産しないと、必要な生産数がまかなえないラインで、あくまでも目標のサイクルタイムとなります。
目標サイクルタイムは、以下の計算式で求められます。
・目標サイクルタイム=ライン稼働時間÷(必要生産量数÷良品率) |
このとき、ラインの停止時間はしっかりと差し引いて、実稼働時間を計算しましょう。必要生産数は、需要予測から今後の生産量を見込みます。最大値の時間間隔と目標とする時間間隔がわかったら、実際に測定した時間と照らし合わせていきましょう。
ピッチダイアグラムの作成
ラインバランスを可視化するためにグラフを作成します。ラインバランス分析で使われるのは、「ピッチダイアグラム」というグラフです。
縦軸には各作業ステーションの作業時間、横軸にはそれぞれの作業ステーションを並べましょう。グラフからは、各作業ステーションにおける作業時間を一覧できるようにします。
縦軸には、測定した工程、または作業者を並べて、それぞれの作業時間を棒グラフで表します。次に、ピッチタイムと目標サイクルタイムを棒グラフの時間軸に記載すればピッチダイアグラムの完成です。
これらを1つの表にまとめて可視化すると、ラインのバランスがひと目でわかるため、課題を客観的に把握できるようになります。
例えば以下のピッチダイアグラムでは、工程1に時間がかかっており、ボトルネック工程であることがわかります。工程の作業時間にばらつきがあり、工程2、3には待ち時間が発生してしまっているのがわかります。
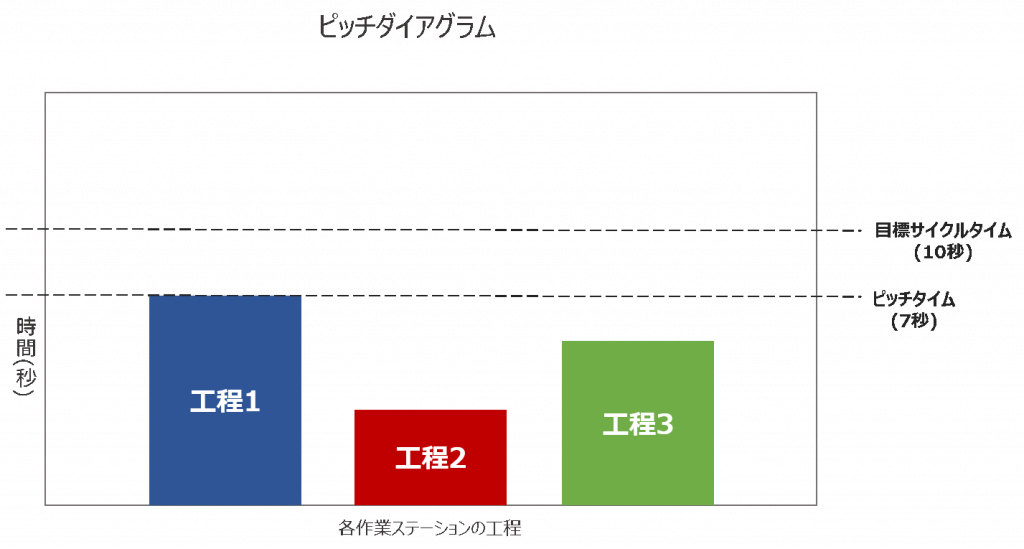
問題点の発見・改善
ピッチダイアグラムでは、どの工程で一番時間がかかっているか、つまりボトルネックになっている箇所が一目瞭然でわかります。
ボトルネックを把握できたら、その工程を早くするにはどうすれば良いかを考えて改善します。1つのボトルネックを解消したら、次は2番目にボトルネックになっていた工程を見直す…といったように、解消していきましょう。
例えば、工程1が目標サイクルタイムを超えていた場合、工程1の処理速度を上げる工夫をする、他の工程に業務の一部を分配するなどの改善が考えられます。
移り変わるボトルネックを把握し、改善や対策を繰り返すことで全体のバランスが整い、生産性が向上していきます。
ただし、製品や作業者によってボトルネックとなる工程は変化する場合があります。1つの製品や1人の作業者だけで判断せずに、状況分析を重ねたうえで改善を進めることが大切です。
このように、ラインバランシングは1度の測定や分析だけでなく、何度も分析を繰り返すことで精度が高まっていきます。
「ラインバランシングの手順はわかっているけれど、人手が足りず改善に着手できていない…」
「1度分析はしてみたものの、データ運用にまで手が回らない」
このような現場では、細かな工程を可視化・分析できる生産スケジューラの導入がおすすめです。
生産スケジューリングを最適化できれば、製造リードタイムの削減やリスクマネジメントはもちろん、短納期の実現や対応力向上による競争力の強化にもつながります。
以下のページではボトルネックの発見や改善に役立つ高精度な生産スケジューラについてや、導入して得られた効果も詳しくご紹介しています。
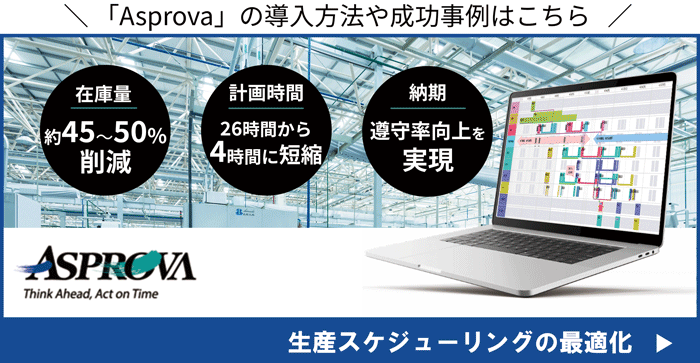
おわりに
ラインバランシングは、生産ラインの作業量を均等化して生産性を向上し、全体管理を最適化できます。ロスタイムを削減して業務効率を上げるためにも、ご紹介した手順でボトルネックを発見して、生産リードタイムの短縮を目指してみてください。
生産管理の最適化のみならず、継続的な分析・運用に取り組みたい場合は、正確なデータ分析や運用が容易に行える生産スケジューラの導入がおすすめです。ライン生産の運用性アップを目指している方は、ぜひ検討してみてはいかがでしょうか。

コラム編集部

最新記事 by コラム編集部 (全て見る)
- なぜこの2社は計画のブレを最小限にできたのか?精度向上のカギを解説 - 2025年7月2日
- “半日が10分に短縮”も可能に!属人化を脱し、計画作成を効率化した方法とは? - 2025年7月2日
- “なんとなく管理”からの脱却!デンカが語る、見える化による現場改善ストーリー - 2025年7月2日