かんばん方式とは?種類や流れを分かりやすく解説
2024.09.09A0 生産管理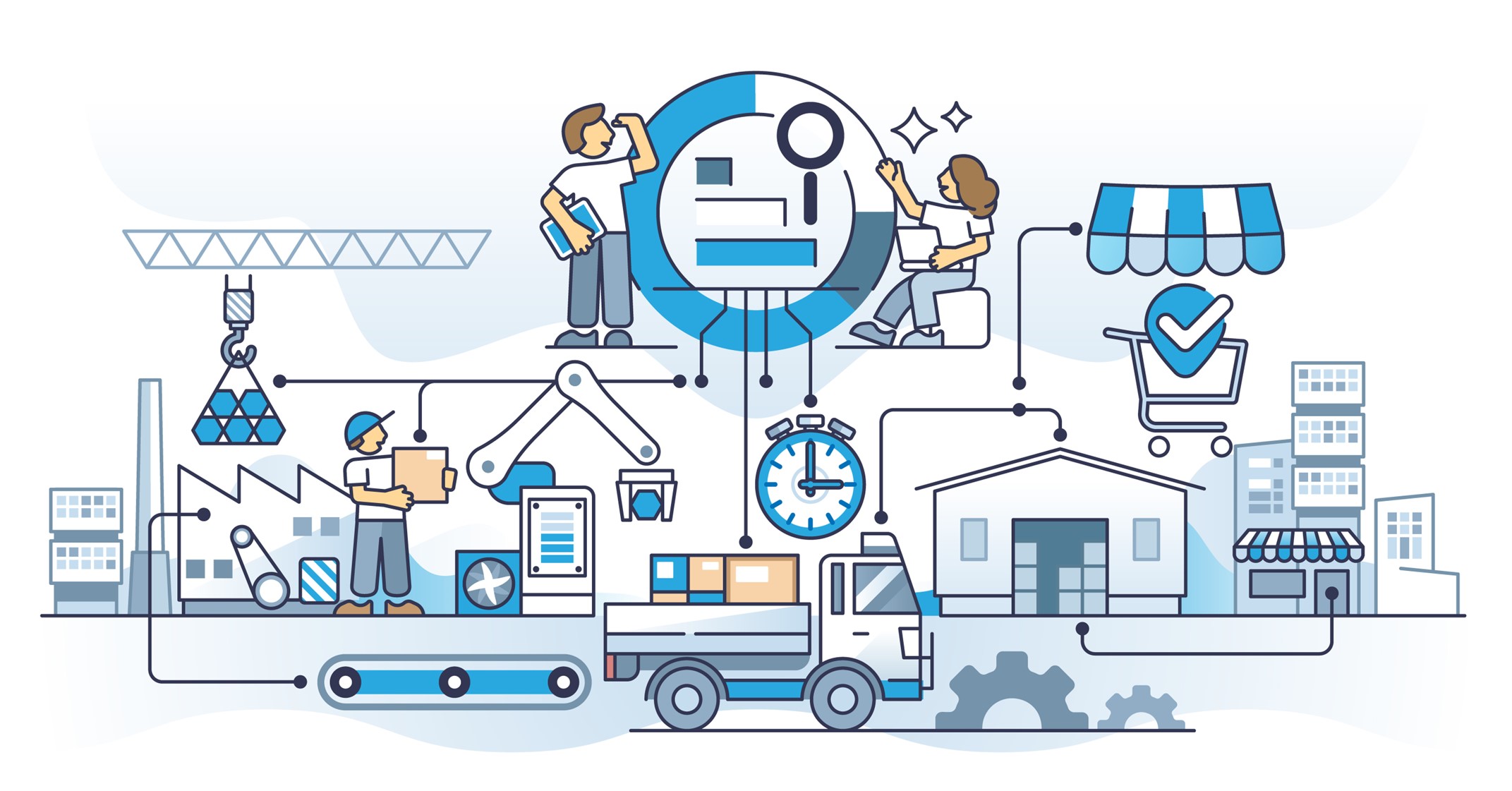
「カンバン方式とは、なんなのだろうか」「業務効率化のための良い方法はあるのか」と悩んでいる製造現場の方も多いでしょう。カンバン方式は「必要なもの」を「必要な時」に「必要な分」だけ製造し、過不足のない生産を可能にする仕組みで、在庫管理の最適化や業務効率化の実現に欠かせません。本記事では、カンバン方式の基礎知識からメリット・デメリット、そして生産スケジューラとの連携による価値の最大化について詳しく解説します。
【目次】
■カンバン方式とは?
■カンバン方式の役割
■カンバン方式のメリット
■カンバン方式のデメリット
■カンバン方式を導入する流れとは
■生産スケジューラでカンバン方式の価値を最大化
カンバン方式とは?
カンバン方式は、「必要なもの」を「必要な時」に「必要な分」だけ製造し、過不足のない生産を可能にする仕組みです。この仕組みはトヨタ自動車が生み出した生産システムで、ジャストインタイムを実現するための重要な要素の1つです。部品1つひとつに「カンバン」という商品管理カードが付いており、部品を使用するとカンバンが外れます。外れたカンバンの数が、足りない部品の数を示します。カンバンに記載された情報を基に部品を作るという流れを繰り返すことで、ムダなく製造が行えるのです。カンバンには、商品名、品番、仕入れコードなどの詳細情報がまとめられています。近年は、紙のカードが使用される従来のカンバン方式に加え、電子カンバンの導入も増えています。
カンバン方式の成り立ち
カンバン方式が1963年に確立されるまでは、アメリカの自動車産業では、プッシュ型と言われるMRPの生産方式が主流でした。しかし当時の日本は裕福ではなかったため、MRPはシステムが高額で在庫を多く抱えるデメリットがあり、断念せざるを得ませんでした。そこで生み出されたのがカンバン方式です。必要なものを必要な時に必要な分だけ作るという、シンプルで分かりやすい仕組みは、製造業だけでなくプロジェクトの管理方法としても応用されています。
トヨタの生産方式におけるカンバン方式の軸
トヨタ自動車が考案したカンバン方式は、「自働化」と「ジャストインタイム」の2つを軸に仕組みを確立しています。自働化とは、工場ラインに異常が発生したら、機械をただちに停止し、不良品を作らないという考え方です。ジャストインタイムとは、各工程で必要なものだけを作り、余分な在庫を持たずに滞りなく生産するという方式です。トヨタ自動車は、この2つの考え方に基づいた生産方法で、顧客のニーズを満たした高品質な車を手際よく作ることを実現しています。
カンバンの種類について
カンバンの種類は、以下のとおりです。
種類 | 詳細な分類 | 説明 |
---|---|---|
仕掛けカンバン | 工程内カンバン | 後工程に引取られた量を、引取られた順番に生産するように仕掛けるカンバン |
信号カンバン | ロット生産工程に用いられ、段取り替えが必要なロット生産工程が後補充生産する製品のそのロットの量を指示するカンバン | |
引き取りカンバン | 工程間引き取りカンバン | 後工程が前工程から必要なものを必要な時に必要な量だけ引き取るためのカンバン |
外注部品納入カンバン | 後工程が前工程から必要なものを必要な分だけ引き取るために使用するカンバン |
上記は、カンバン方式で使用される仕掛けカンバンと引き取りカンバンの表です。分かりやすく、種類と機能をまとめました。仕掛けカンバンは補充生産を指示するために使用され、工程内カンバンと信号カンバンに分けられます。一方、引き取りカンバンは後工程が前工程から部品や製品を引き取るためのツールで、工程間引き取りカンバンと外注部品納入カンバンがあります。これらのカンバンを適切に運用することで、カンバン方式の効果的な実施が可能になります。
カンバン方式の流れ
カンバン方式の主な流れは、以下のとおりです。
- 顧客から注文を受ける
- 後工程の担当者が、前工程にカンバンを渡す
- 前工程で、カンバンの数だけ生産する
この流れを「引き取りカンバン」と「仕掛けカンバン」に分けて詳しく説明します。
引き取りカンバンの流れ
1.後工程が前工程から必要な部品や製品を引き取る際、引き取りカンバンを前工程に渡す
後工程の担当者が、前工程に引き取りカンバンを渡します。このカンバンにより、前工程がどの部品や製品をどれだけ生産するかが指示されます。
2.前工程は、引き取りカンバンの数だけ生産し、後工程に供給する 前工程は、引き取りカンバンに記載された数だけ部品や製品を生産します。生産された部品や製品は、後工程に供給されます。
仕掛けカンバンの流れ
1.後工程が部品や製品を使用すると、仕掛けカンバンが外れる
後工程で部品や製品が使用されると、対応する仕掛けカンバンが外れます。これにより、補充が必要であることが示されます。
2.外れた仕掛けカンバンの数が、補充すべき部品や製品の数を示す
外れた仕掛けカンバンの数は、前工程が補充生産すべき部品や製品の数を示します。前工程はこの情報を基に補充生産の計画を立てます。
3.前工程は、仕掛けカンバンの情報を基に、指示された数だけ生産する
前工程は、外れた仕掛けカンバンの情報に基づいて、生産すべき部品や製品の数を決定します。指示された数だけ部品や製品を生産し、在庫や後工程に供給します。
このようにカンバン方式は、カンバンを用いて必要なものを必要な時に必要な分だけ生産することで、効率的な生産を実現しています。
カンバン方式の役割
カンバン方式の役割は、以下の3つです。
- 生産量や運搬の情報を指示
- 余剰在庫の防止
- 不良品の防止
これらは生産現場における情報の可視化、在庫管理の最適化、品質管理の徹底に重要な役割を果たします。
生産量や運搬の情報を指示
カンバンには「何を」「いつ」「どれだけ」作るのか、「どこへ」持っていくのかが明記されています。この情報が一目で分かるため、作業者は迅速かつ正確に作業を進められるのです。また、カンバンに記載された情報に従って作業を行うことで、現品間違いのミスを防止できます。カンバンは、生産現場における情報の可視化に大きく貢献しています。作業者は、カンバンを見れば、自分が何をすべきかを即座に理解することが可能です。この可視化により、作業の効率が上がり、ミスの発生率も低下します。
余剰在庫の防止
カンバン方式では、カンバンが届いた時だけ生産を行います。そのため、必要以上に生産することがなく、余剰在庫の発生を防ぐことが可能です。また、完成品を補完する倉庫の整備や、原材料の在庫管理に要する労力とコストを最小限に抑えられます。 従来の大量生産方式では、需要予測に基づいて生産を行うため、予測が外れた場合、大量の在庫を抱えてしまう恐れがありました。一方カンバン方式では、実際の需要に応じて生産を行うため、在庫量を適正に保てます。
不良品の防止
カンバン方式では「良品のみを次の工程に渡す」というルールを設定しておくことで、不良品の流出を防止できます。万一不良品が発生した場合でも、その時点で生産を停止し、再発防止策を講じることが可能です。品質管理の徹底は、カンバン方式の重要な役割の1つです。不良品を後工程に流出させないことで、最終製品の品質を高い水準で維持できます。また、不良品の発生原因を迅速に特定し、対策を講じることで、品質改善のPDCAサイクルを回せます。
カンバン方式のメリット
カンバン方式のメリットは、以下の3つです。
- 過剰在庫の防止
- 情報管理の安定化
- コミュニケーションが取りやすくなる
これらのメリットを活かすことで、生産性の向上、コスト削減、品質改善など、企業の競争力強化に役立てられます。
過剰在庫の防止
カンバン方式では、製品1つひとつにカンバンを付け、その製品が使用されるとカンバンが外れます。外れたカンバンの数だけ製品を製造するため、作り過ぎを防げます。この仕組みにより、過剰在庫を抑制し、在庫管理コストを削減可能です。また、カンバン方式は需要に応じた生産を可能にします。必要な製品を必要な時に必要な分だけ生産するため、市場の変化に柔軟に対応可能です。これにより、在庫リスクを最小限に抑えつつ、顧客ニーズに迅速に応えられます。
情報管理の安定化
カンバン方式では、必要な情報を入力するフォーマットを統一できます。これにより、担当者によって情報の入力方法が異なるのを避けられ、誰が見てもひと目で情報の確認が可能です。その結果、プロジェクトの進捗管理がスムーズになります。
情報の可視化は、カンバン方式の大きなメリットの1つです。カンバンに記載された情報は、全てのメンバーが共有できるため、作業の重複や抜け漏れを防げます。また、情報の更新もリアルタイムで行われるため、常に最新の状況を把握できます。
コミュニケーションが取りやすくなる
カンバン方式で作業を進行することにより、メンバーの作業状況が把握しやすくなります。これにより、作業の遅れを早期に発見でき、迅速にリカバリー策を講じることが可能です。その結果、チームのメンバーが協力し合い、プロジェクトを成功に導けるのです。カンバン方式は、メンバー間のコミュニケーションを促進する効果もあります。カンバンを介して作業の依頼や引き継ぎを行うことで、メンバー間の連携がスムーズになります。このように、カンバン方式はチームのコミュニケーションと協力を促進し、プロジェクトの成功に貢献するのです。
カンバン方式のデメリット
カンバン方式のデメリットは、以下3つです。
- 欠品リスクを高めやすい
- 現場の負担が大きくなりやすい
- タスクの重要性を把握しにくくなる
カンバン方式は生産効率の向上や在庫管理の最適化に役立つ一方で、いくつかのデメリットも抱えています。デメリットを理解しておくことで、カンバン方式の導入や運用をより効果的に行えます。適切な対策を講じることで、デメリットを最小限に抑えながら、カンバン方式のメリットを最大限に活かすことが重要です。
欠品リスクを高めやすい
カンバン方式では、必要な分だけ生産を行うため、万一作業工程にトラブルが発生した場合、欠品のリスクが生じる可能性があります。欠品が発生すると、売上減少や受注機会の損失につながるリスクも考えられます。この欠品リスクを軽減するためには、安全在庫の設定や、生産スケジューラの導入による「計画生産」が有効です。安全在庫を適切に設定することで、トラブル発生時の欠品を防げます。
現場の負担が大きくなりやすい
カンバン方式は、不良品が出ないことを前提とした生産方式です。不良品が発生すると、欠品により在庫管理に影響が出ます。そのため、不良品を防ぐために、プロジェクトの進行ルールが厳しくなったり、メンバー間のコミュニケーション強化が求められたりと、作業者の負担が大きくなる可能性があります。この現場の負担増加を防ぐためには、生産スケジューラの導入による「負荷の見える化」が有効です。生産スケジューラを用いることで、作業者の負荷が今後どのように変動するかを予測し、負荷の偏りを事前に察知できます。これにより、適切な対策を講じることで、作業者の負担を軽減できます。
タスクの重要性を把握しにくくなる
カンバン方式はタスクの量や状況を把握し、対策を立てられる生産方式です。しかしタスクの重要度を見える化しにくいという特徴があります。タスクの優先順位や進捗状況などの管理が不足すると、作業効率が低下する恐れがあります。このタスクの重要性の把握困難を解消するためには、生産スケジューラの導入による優先順位調整が有効です。生産スケジューラを用いることで、タスクの優先順位を明確にし、進捗状況を可視化できます。特に、少量多品種生産や需要変動が多い場合には、生産スケジューラの導入を検討するとよいでしょう。
このようにカンバン方式にはメリットだけでなく、デメリットもあります。これらのデメリットを克服するためには、安全在庫の設定や生産スケジューラの導入など、適切な対策を講じる必要があります。
カンバン方式を導入する流れとは
カンバン方式を導入する際は、5つのステップを踏むことが重要です。また、タスク管理を効果的に行うためのコツについても理解しておきましょう。
カンバン方式を導入時の5つのステップ
ステップ1.タスクの見える化とカテゴリ分け: プロジェクトに関連する全てのタスクを洗い出し、カテゴリごとに分類します。これにより、プロジェクト全体の作業内容が明確になり、タスクの優先順位付けがしやすくなります。
ステップ2.ワークフローの設計:
カテゴリ分けしたタスクを元に、最適なワークフローを設計します。各タスクの依存関係や順序を考慮し、作業の流れを視覚化します。これにより、プロジェクトの進行状況が把握しやすくなります。
ステップ3.作業量と制約の設定:
各タスクの作業量を見積もり、制約条件を設定します。リソースの割り当てや期限の設定など、現実的な計画を立てることが重要です。これにより、プロジェクトの遅延リスクを最小限に抑えられます。
ステップ4.進捗管理の追跡:
プロジェクトの進行状況を定期的に追跡し、遅延や問題点を早期に発見します。カンバンボードを活用し、タスクの状況を可視化することで、チーム全体で進捗状況を共有できます。カンバンボードとは、タスクの割り当てや期日などの情報を視覚的に整理し、チームで常に最新の情報を共有できるシステムです。
ステップ5.ワークフローの見直しと改善:
プロジェクトの進行に合わせて、ワークフローを継続的に見直し、改善します。ボトルネックの特定や作業の効率化など、カイゼンの考え方を取り入れることが重要です。
カンバン方式でタスク管理を行うコツ
カンバン方式でタスク管理を行うコツは、以下の4つです。
- タスクは具体的に作成する
- タスクの粒度に差を出さない
- シングルタスクで行う
- スケジュール管理ができるツールと併用する
このようなコツを押さえておくことで、カンバン方式を効果的に運用し、プロジェクトの効率化と品質向上を実現できます。
タスクは具体的に作成する
タスクの期限や内容、優先順位を明確に定義することで、全員がプロジェクトの状況を正確に把握できるようになります。これにより、確認作業に要する工数を削減できます。
タスクの粒度に差を出さない
タスクごとの負荷をなるべく均等にすることで、メンバーが自分の作業に集中しやすくなり、製品の品質向上が期待できます。適度にタスクを振り分けることが重要です。
シングルタスクで行う
マルチタスクにすると、カンバン方式で整理したタスクがより複雑になり、メンバーのタスクを把握しにくくなります。メンバー間の連携が取れないと、タスクの見直しや割り振りの機会を逃してしまい、作業効率が低下する可能性があります。作業に取り掛かりやすくし、チームのコミュニケーションを活発化するためにも、シングルタスクでの運用がおすすめです。
スケジュール管理ができるツールと併用する
カンバン方式の弱点である「時系列ごとのタスク管理ができない」点を補うために、スケジュール管理ツールとの併用が有効です。これにより、作業の効率化と品質向上を図れます。特に生産スケジューラは在庫削減やリードタイムの短縮、生産工程の見える化など、さまざまな効果が実証されているシステムです。生産プロセスの最適化を目指す企業におすすめのツールといえます。
生産スケジューラでカンバン方式の価値を最大化
カンバン方式は、在庫管理の効率化やジャストインタイム生産の実現に役立つ一方で、需要変動が大きい環境や多品種少量生産の場面では、欠品リスクが高くなりやすい特徴があります。このような場面では、生産スケジューラの活用が効果的です。
カンバン方式が適用しづらい工程では、生産スケジューラを用いて需要予測やリソースの制約を考慮した最適な生産計画を立てることで、生産の流れをよりスムーズに調整できます。また、カンバン方式が適用できる工程ではその特性を活かしつつ、他の工程ではスケジューラを併用することで、現場の実態に即した柔軟な対応が可能です。
これにより、在庫の最適化やリードタイムの短縮、生産効率の向上、計画の可視化など、多くのメリットが期待できるでしょう。カンバン方式と生産スケジューラを組み合わせて使うことで、それぞれの強みを活かし、効率的な生産管理が実現します。生産スケジューラ導入によって、どのような業務改善が実際に達成されたのかは、こちらのページをご覧ください。

コラム編集部

最新記事 by コラム編集部 (全て見る)
- なぜこの2社は計画のブレを最小限にできたのか?精度向上のカギを解説 - 2025年7月2日
- “半日が10分に短縮”も可能に!属人化を脱し、計画作成を効率化した方法とは? - 2025年7月2日
- “なんとなく管理”からの脱却!デンカが語る、見える化による現場改善ストーリー - 2025年7月2日