MRPとは?メリットやMRP2やAPSとの違いをわかりやすく解説
2024.09.09A0 生産管理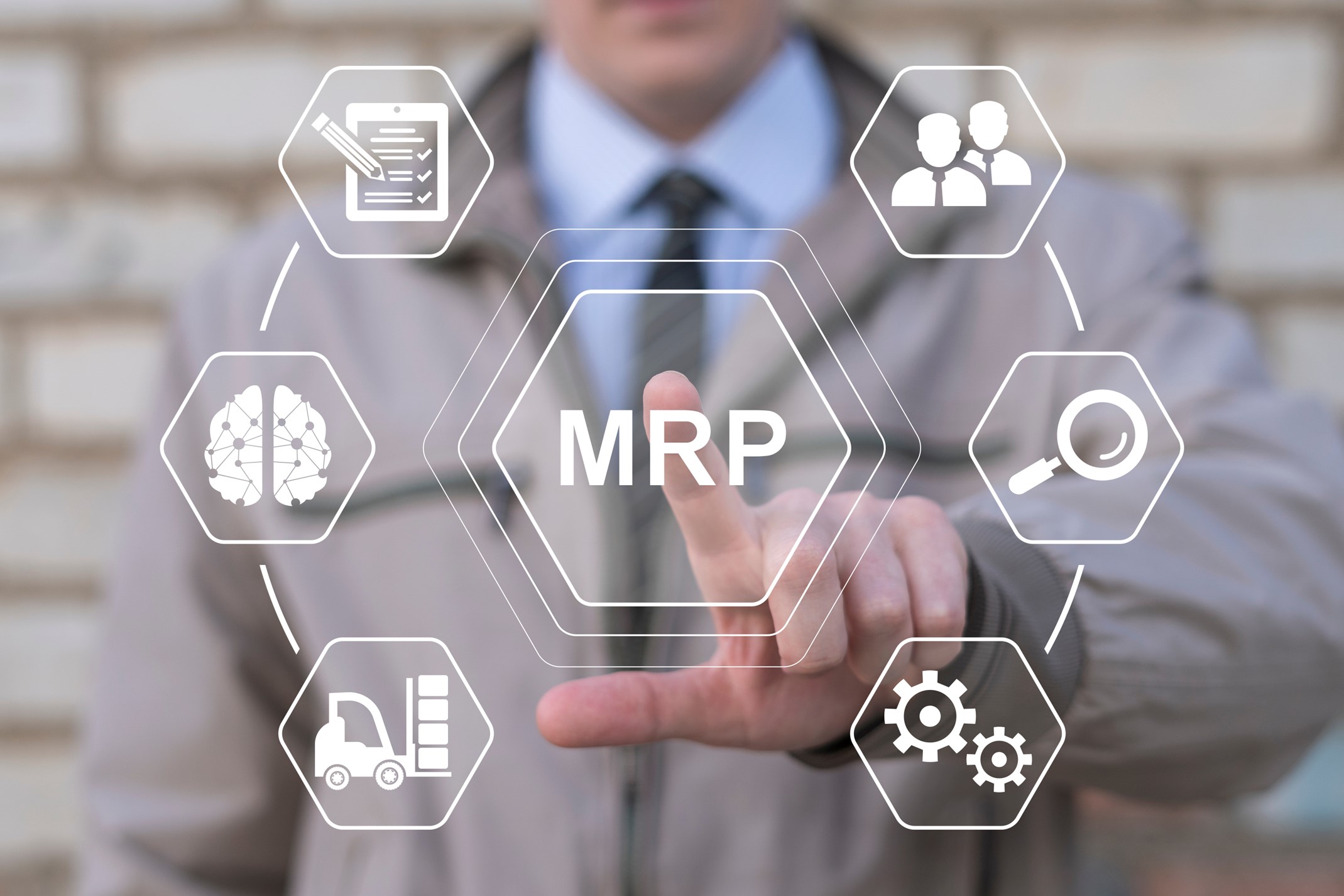
「MRPを業務に取り入れたいけどよく分からない」「MRPで業務を効率化したい」と思っている方も多いでしょう。
MRPは在庫管理の最適化や生産性向上に効果的ですが、計画変更時の手間やデータ精度への影響といった課題もあります。本記事では、MRPの概要やメリット・デメリットに加え、生産スケジューラとの統合による生産管理の効率化について詳しく解説します。
【目次】
■資材所要量計画「MRP」とは
■MRPを活用する3つのメリットと2つの課題
■2種類の部品表について
■MRPの進め方
■おわりに
資材所要量計画「MRP」とは
資材所要量計画「MRP」とは、生産計画に基づいて必要な資材の数量を管理する手法です。MRPを適切に活用できれば在庫リスクを低減させ、生産性の向上にも役立つツールとなります。MRPは、「必要なものを」「必要な時に」「必要なだけ」購入・製造するために、生産計画を基に資材の必要数を計算し、購入時期を決定します。この手法は、製造業の在庫管理などに広く活用されています。
MRPに必要なもの
MRPで必要資材の数量を算出するためには、次の3点を用意します。
・生産計画
生産する製品についての生産計画を立てます。生産する製品の個数は受注数や需要予測によって算出することができます。
・部品表
製品を作るために、どの部品が、いつまでに、どれくらい必要かを記載した表を作成します。部品表には、部品を作る際のリードタイム(発注から納品に至るまでの時間)など、詳細な情報を記載します。
・在庫情報
製品を作るために必要な部品の数を計算した後、在庫の中に使える部品がどれくらいあるかを確認します。使える部品があった場合は、それに加えてあとどれくらい部品を発注すればいいかを算出します。
MRPとMRP2の違い
MRP2(Manufacturing Resource Planning)は、製造資源計画と呼ばれる手法です。MRPが資材の調達や在庫管理の効率化を目指しているのに対し、MRP2では人員や設備などの生産資源も考慮して計画を立てます。つまり、MRP2は生産全体の効率化を考えて製品計画を立てるのです。
MRP2と生産スケジューラ(APS)の違い
MRP2は資材、人員、設備を含む生産資源を計画する手法であり、全体的な製造プロセスの効率化を目指します。一方、APS(Advanced Planning and Scheduling)は、より高度なアルゴリズムを用いて、スケジューリングの最適化を行うツールです。APSは複雑な製造環境において、短納期や高い変動性に対応するための柔軟性と精度を提供します。MRP2が中長期的な計画を重視するのに対し、APSは日々の生産スケジュールの詳細な最適化を重視するのです。そのため、MRP2とAPSは、製造業における計画と実行の異なる側面に焦点を当てていると言えます。MRP2は全体的な資源の効率的な配分を目指し、APSは日々の生産スケジュールの最適化を通じて、変化する需要や制約に対応するのです。
MRPとERP・JITの違い
MRPは生産管理や在庫管理に特化した手法であるのに対し、ERPは企業全体の基幹業務を統合的に管理するための手法やシステムです。一方、JITは後工程から前工程に対して必要な原材料を指示して取り寄せるプル型の手法であり、MRPとは工程の流れが逆になります。それぞれの特徴や違いについて詳しく見ていきましょう。
MRPとERPの違い
MRPは生産管理や在庫管理を計算する手法であるのに対し、ERPはヒト・モノ・カネ・情報を管理する手法です。ERPは「Enterprise-Resource-Planning」の略語で、日本語では企業資源計画と呼ばれます。生産管理や在庫管理を含め、企業全体の基幹業務を統合的に管理するための手法やシステムをERPと捉えるとよいでしょう。
MRPとJITの違い
MRPは製造工程の前工程から後工程に対して、原材料の発注数やタイミングを指示するプッシュ型(=押し出し方式)の手法です。対するJIT(ジャスト・イン・タイム)は、後工程から前工程に対して必要な原材料を指示して取り寄せるプル型(=引っ張り方式)の手法です。工程は前後しますが、どちらも「必要なものを/必要な時に/必要な分だけ手配する」という理論は共通しています。
MRP、ERP、JITは、いずれも生産管理や在庫管理の効率化を目的とした手法です。しかし適用範囲や工程の流れに違いがあります。MRPは生産管理や在庫管理に特化していますが、ERPは企業全体の基幹業務を統合的に管理するための手法です。一方、JITは後工程からの引っ張り方式で必要な原材料を手配します。これらの手法を理解し、自社の業務に合った方法を選択・適用することが重要です。
MRPを活用する3つのメリットと2つの課題
MRPを活用することで、以下の3つのメリットが得られます。
- 在庫管理の効率化
- 在庫コストや資材コストの削減
- 生産性の向上
一方で、計画変更時の手間や各種データの精度が結果に影響するという2つの課題もあります。これらのメリットと課題について詳しく見ていきましょう。
メリット1:在庫管理が効率化される
MRPは生産計画に基づいて必要な資材の所要量を算出するため、在庫の過不足を防げます。過剰在庫はコストの増加や資材の劣化につながり、在庫不足は欠品などのトラブルを引き起こすでしょう。しかしMRPを活用することで、適正な在庫レベルを維持できるようになります。また、MRPは資材の発注タイミングや発注量の最適化が可能です。これにより、資材の発注や納品に関連する業務の効率化も期待できます。在庫管理の自動化や最適化により、人的エラーの削減やリードタイムの短縮にもつながります。このようにMRPを活用することで在庫管理が効率化されるのです。
メリット2:在庫コストや資材コストを削減できる
在庫の過不足を防ぐためには、MRP(資材所要計画)だけでなく、スケジューラの活用が重要です。スケジューラを組み合わせることで、より精密な在庫管理が可能になり、在庫コストを抑えることができます。過剰在庫は保管スペースや保険料、減価償却費などのコストを増加させる一方で、在庫不足は機会損失や緊急輸送費用といった追加コストを生むこともあります。
MRPとスケジューラを併用することで、適切なタイミングで必要な資材を手配でき、これらのコストを抑えることができます。さらに、大量発注の割引や、複数の仕入れ業者からの見積もり比較によって、資材をより安く調達できる可能性も高まります。資材の調達コストが削減されることで、製品の原価低減や利益率の向上が期待できるでしょう。これにより、在庫コストの削減だけでなく、キャッシュフローの改善にもつながります。
メリット3:生産性向上につながる
MRPは生産に必要な資材や部品の適切な管理を可能にし、在庫の最適化を実現することが可能です。そのため生産計画や調達プロセスが効率化され、生産ラインの停滞や欠品のリスクが軽減されます。資材不足による生産ラインの停止は、生産性の低下や納期遅延などの問題を引き起こしますが、MRPを活用することで、これらのリスクを最小限に抑えられるのです。また、MRPはリードタイムの短縮や生産計画の精度向上にも貢献します。資材の調達リードタイムを短縮することで、市場の需要変化に迅速に対応できるようになります。さらに、正確な生産計画を立てることで、生産資源の最適化や生産スケジュールの効率化が可能です。これにより、生産性の向上だけでなく、品質の安定化や従業員の士気向上にもつながるといえます。
課題1:計画変更時の手間がかかる
MRPを運用する上で、計画変更や発注変更、在庫変動などにスムーズに対応できないと、生産ラインが停滞したり、資材の過不足が発生したりするリスクがあります。これらの問題は納期遅延や在庫コストの増加、品質低下などにつながる可能性があるため、MRPの運用効率を維持するためには、柔軟な変更対応が必要です。そのためには、部門間の連携やリアルタイムでの情報共有が不可欠です。連携がとれていないと運用が滞ってしまうので、情報共有のための仕組みづくりや社内コミュニケーションの活性化に取り組むことが重要です。
課題2:各種データの精度が結果に影響する
MRPは、生産計画や部品表、在庫管理情報などのデータを基に資材の所要量を算出する手法です。そのため、生産計画や部品表など基となるデータの精度が低いと、思うような効果が得られない可能性があります。たとえば、部品表の粒度が粗かったり、マスターデータが古いままだったりすると、正確な所要量計算ができません。
課題を解消するためには、情報共有しやすい環境の整備・仕組み化を行うことや、部品表(BOM)や生産計画の精度の見直しを行うことが重要です。こうした取り組みを通じて、MRPの運用をより効果的なものにしていけるでしょう。
2種類の部品表について
MRPは部品表を用いて製品に必要な部品の数を計算するため、部品表を適切に運用することが重要になります。MRPで使用される部品表は、サマリー型とストラクチャ型の2つに分類できます。
・サマリー型部品表
サマリー型部品表とは、製品に必要な部品の種類と数を一覧にしたものです。どの部品をいくつ使っているかが一目で分かるのが特徴です。製品を作るために必要となる部品の数や種類が少ない場合に使用されます。
・ストラクチャ型部品表
ストラクチャ型部品表とは、製品に必要な部品を組み立ての段階ごとに階層に分けて記載する方法です。組み立ての工程(業務)が多く、複雑な製品などに使われます。
MRPの進め方
MRPを進める3つのステップは以下のとおりです。
- 1.生産計画を策定
- 2.部品構成表の作成
- 3.各種資材表の発注
それぞれのステップで必要な情報を収集・分析し、適切な判断を下していくことが重要です。
1.生産計画を策定
生産計画とは、製品の製造に必要な資材・設備・人員などの資源をどのように配分するかを計画したものです。MRPを取り入れる際は、生産に必要な材料を「必要な時に」「必要なだけ」確保できるように計画を立てます。生産計画は、過去の受注・製造データなどを参考に需要予測を行った上で立案しましょう。
2.部品構成表の作成
部品構成表とは、製品を構成する部品や材料のリストのことで、製品の設計図や製造工程を基に作成します。MRPでは部品構成表に基づいて必要な資材の所要量を算出するため、適切な粒度の部品構成表を作成する必要があります。
3.各種資材表の発注
生産計画と部品構成表ができたあとは、現時点の在庫量を差し引き、資材の発注を行いましょう。これを「発注計画」と呼びます。所要量を算出し、発注点と発注量を決定したあとに、発注先の決定や発注書の発行を行います。この一連のプロセスを通じて、必要な資材を適切なタイミングで調達することが可能です。
以上の1~3の流れを実践し、課題を都度ブラッシュアップしてMRP運用の精度を高めていくことが大切です。MRPは一朝一夕で完璧に運用できるものではありません。継続的な改善努力を積み重ねることで、徐々に効果を実感できるようになるでしょう。
おわりに
MRPは生産計画に基づいて必要な資材の数量を管理する手法であり、在庫管理の効率化、在庫コストや資材コストの削減、生産性の向上といったメリットがあります。一方で、計画変更時の手間や各種データの精度が結果に影響するという課題もあるため、情報共有しやすい環境の整備・システム化、部品表(BOM)、生産計画の精度の見直しが重要です。さらに、MRPと生産スケジューラを統合することで、生産プロセス全体の管理がより効率化されます。生産スケジューラは生産能力やリソースの制約を考慮して生産計画を作成し、MRPは材料の需要と在庫を最適化します。このような連携によって、生産スケジュールと材料の供給が最適化され、生産プロセス全体がスムーズに運用されるのです。生産スケジューラ導入によって具体的にどのような業務改善が実現したのかはこちらのページをご確認ください。

コラム編集部

最新記事 by コラム編集部 (全て見る)
- なぜこの2社は計画のブレを最小限にできたのか?精度向上のカギを解説 - 2025年7月2日
- “半日が10分に短縮”も可能に!属人化を脱し、計画作成を効率化した方法とは? - 2025年7月2日
- “なんとなく管理”からの脱却!デンカが語る、見える化による現場改善ストーリー - 2025年7月2日