もう失敗しない!MRPとスケジューラで精度100%の原材料調達計画
2025.05.21A0 生産管理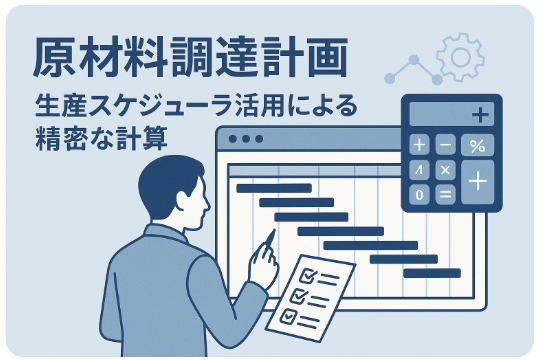
原材料調達計画とは、製品の生産に必要な原材料を「いつ」「どれだけ」手配するかを決める計画です。この計画は、MPS(基準生産計画)で決まった製品の生産数量をもとに、必要な原材料の種類と数量と発注タイミングを導き出すものです。
たとえば、MPSで「来週、製品Aを200個生産する」と決まれば、その製品Aに必要な部品や原材料を今週中に手配する必要があります。こうした段取りを誤ると、部材不足で生産が止まったり、逆に在庫が積み上がったりと、現場に混乱が生じます。
原材料調達計画の重要性
調達計画の精度が低いと、以下のような問題が発生します。
- 供給の遅延による生産ストップ
- 在庫過剰によるコスト増
- 急な対応に伴う業務の混乱
これらのリスクを未然に防ぐために、正確で柔軟な調達計画が不可欠です。特に、多品種少量生産の現場では、部材の入荷タイミングが命運を握ります。
MRPを活用した調達計画の立て方
MRP(資材所要量計画)は、MPSに基づいて原材料の所要量を算出するシステムです。構成表(BOM)や在庫情報、リードタイムなどをもとに、必要な調達量と時期を計算します。
MRPの流れは、以下の通りです。
- MPSを計画:どの製品をいつ、どれだけ作るかを決定します
- BOMによる原材料への分解:製品に必要な部材や原材料を洗い出す
- 正味所要量の算出:手持ち在庫や発注済みの分を差し引いて正味所要量を算出します
- 発注時期の決定:リードタイムを考慮し、発注タイミングを確定します
MRPの課題
MRPは非常に便利な仕組みですが、以下のような問題があります。
- 固定リードタイムで原料の必要なタイミングを計算するため、結果が不正確
- 製造工程の遅れや急な注文変動に対応しづらい
- 部材の納期変更など、現場の細かな動きに追従できない
こうした課題を補うのが、生産スケジューラです。
生産スケジューラ活用による精密な調達計画
生産スケジューラは、製造現場の作業や工程を時間軸で管理するシステムです。設備の空き状況や作業員の負荷、工程ごとの処理能力などを考慮して、生産計画を最適化します。生産スケジューラの出力から調達計画を作成すると、次のようなメリットがあります。
- MPSや生産スケジュールが変更されると、原材料の発注量・タイミングが自動的に再計算されます
- 計画と実績のズレに応じて、リアルタイムな調達計画の変更が可能になります
これにより、調達の「ズレ」が減り、現場全体のリズムが整いやすくなります。
実務での活用ポイント
MRPもスケジューラも、BOM、在庫、リードタイムなどのデータが正しくなければ機能しません。定期的な見直しとメンテナンスが重要です。調達担当者がスケジューラの操作や情報にアクセスできるようにし、現場の状況をリアルタイムで共有する体制が求められます。
特急対応や仕様変更といった突発イベントへの対応のしかたも、あらかじめルールを決めておく必要があります。
まとめ
原材料調達計画は、生産現場を支える極めて重要な業務です。従来のMRPではなく、生産スケジューラを活用することで、精度と柔軟性を兼ね備えた調達が実現できます。特に、需要の変化が激しく、人手不足が進む現場では、「計画と現場のズレ」を最小限に抑える仕組みが必要です。スケジューラとの連携により、調達業務は“守り”から“攻め”へと進化します。

コラム編集部

最新記事 by コラム編集部 (全て見る)
- 急な需要変動も怖くない!計画変更を爆速化する秘策とは? - 2025年7月30日
- 「計画作成のバラつきをゼロに」――現場が変わる標準化の成功事例2選 - 2025年7月30日
- 「必要なときに必要な量だけ」――原材料手配のムダをなくした現場改革の実例 - 2025年7月30日