PDCAが回らない理由はここにある!スケジューラ導入で解決する方法
2025.05.21A0 生産管理生産現場では、日々の業務改善が欠かせません。納期遅延の防止、在庫削減、生産効率の向上など、多くの課題に直面する中で、継続的な改善を実現するための有効な手法がPDCAサイクルです。そして、現代の生産現場では、このPDCAサイクルをより迅速かつ効果的に回すために、生産スケジューラが重要な役割を果たしています。
本記事では、PDCAサイクルの基本から、生産スケジューラがどのようにそれを支援し、現場の改善活動に貢献するのかを、わかりやすく解説します。
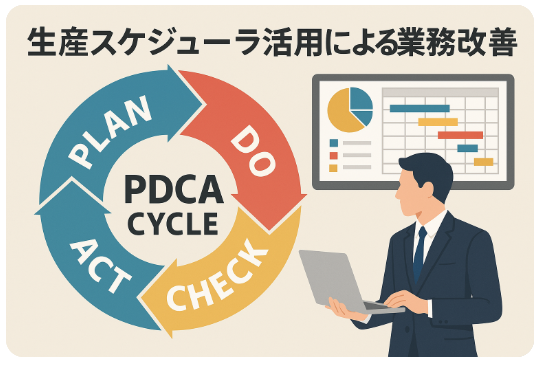
PDCAサイクルの基本
1) Plan(計画) : 生産計画では、受注や需要予測をもとに、何を・いつ・どれだけ作るのかを決定します。ここで重要なのは、設備の稼働状況や人員配置、材料の入荷状況など、あらゆる要素を考慮して、現実的かつ達成可能な計画を立てることです。
2) Do(実行) : 立案した計画に基づいて実際の生産が行われます。このとき、製造指示や作業指示が現場に伝えられ、ラインが稼働します。トラブルや変更が発生した場合でも、現場は柔軟に対応する必要があります。
3) Check(評価) : 計画と実績を比較・分析する段階です。ここでは「計画通りに生産できたか」「納期に遅れはなかったか」「不良品が多く発生していないか」などを確認します。差異があれば、その原因を明らかにすることが重要です。
4) Action(改善) : Checkで明らかになった問題点に対する対策を講じます。この改善結果は、次回のPlanに反映され、PDCAサイクルが再びスタートします。この繰り返しによって、業務の質は徐々に向上していきます。
PDCAサイクルの課題と限界
PDCAサイクルは非常に有効な手法ですが、実際の運用では以下のような課題もあります。
- 計画の立案に時間がかかる
- 計画と実績のズレへの対処が煩雑
- 改善が属人的で再現性に乏しい
これらの課題を解決するために、注目されているのが生産スケジューラの活用です。
生産スケジューラの活用
生産スケジューラは、生産計画を自動で作成し、リソースの最適配分や納期順守のためのスケジュールを計算するソフトウェアです。多くのスケジューラは、以下のような機能を備えています。
- 工程や設備・作業者ごとの負荷を考慮した有限能力の計算
- 設備や作業者の詳細なスケジューリング
- 原材料や部品の在庫の考慮
- ガントチャートによる可視化
これにより、現場の状況を即座に反映した計画が作成できるようになり、以下のようにPDCAサイクルのスピードと精度が大幅に向上します。
生産スケジューラによるPDCAサイクル
1) Plan : 納期や在庫、リードタイム、リソースの負荷状況を考慮した計画を自動的に立案できます。人手では困難だった多変数の最適化が可能になり、より精度の高い計画が短時間で作成可能になります。
2) Do : 作成されたスケジュールは、製造現場に正確かつタイムリーに伝達されます。これにより、段取り替えや優先順位の混乱が減り、現場の実行力が向上します。
3) Check : 実績データを取り込み、計画との差異を自動で分析できます。問題のある工程や遅延の原因を迅速に把握できるため、改善点の特定がスムーズになります。
4) Action : 計画と実績のズレを考慮して、リスケジューリングが可能になります。これにより、PDCAが形式的なサイクルではなく、実効性ある改善サイクルとして定着します。
まとめ
PDCAサイクルは、日々の業務改善を継続的に進めるための強力なフレームワークです。そこに生産スケジューラを組み合わせることで、計画の高度化、実行の安定化、評価の迅速化、改善の自動化が実現します。
属人的な経験や勘に頼るのではなく、データに基づいた改善を積み重ねることで、生産現場の競争力は確実に向上していくでしょう。これからの生産管理において、PDCAとスケジューラの連携は欠かせない要素となるはずです。
最適化AIを搭載した生産スケジューラに関しては、こちらをご覧ください

コラム編集部

最新記事 by コラム編集部 (全て見る)
- 急な需要変動も怖くない!計画変更を爆速化する秘策とは? - 2025年7月30日
- 「計画作成のバラつきをゼロに」――現場が変わる標準化の成功事例2選 - 2025年7月30日
- 「必要なときに必要な量だけ」――原材料手配のムダをなくした現場改革の実例 - 2025年7月30日