無料で試せる生産スケジューラAsprova APS
無料で試せる生産スケジューラAsprova APS
生産スケジューラAsprova APSは製造業の生産資源の有効な時間活用によって、既存業務の問題点を改善し、収益改善まで実現させるという問題解決型のソフトウェアです。まずは無料体験版で基本機能を確認し、次に有料の月単位トライアル版でプロトタイプを作成し、導入決定後に正式版を使ってプロトタイプをアップデートするという流れで無理のない導入が可能です。
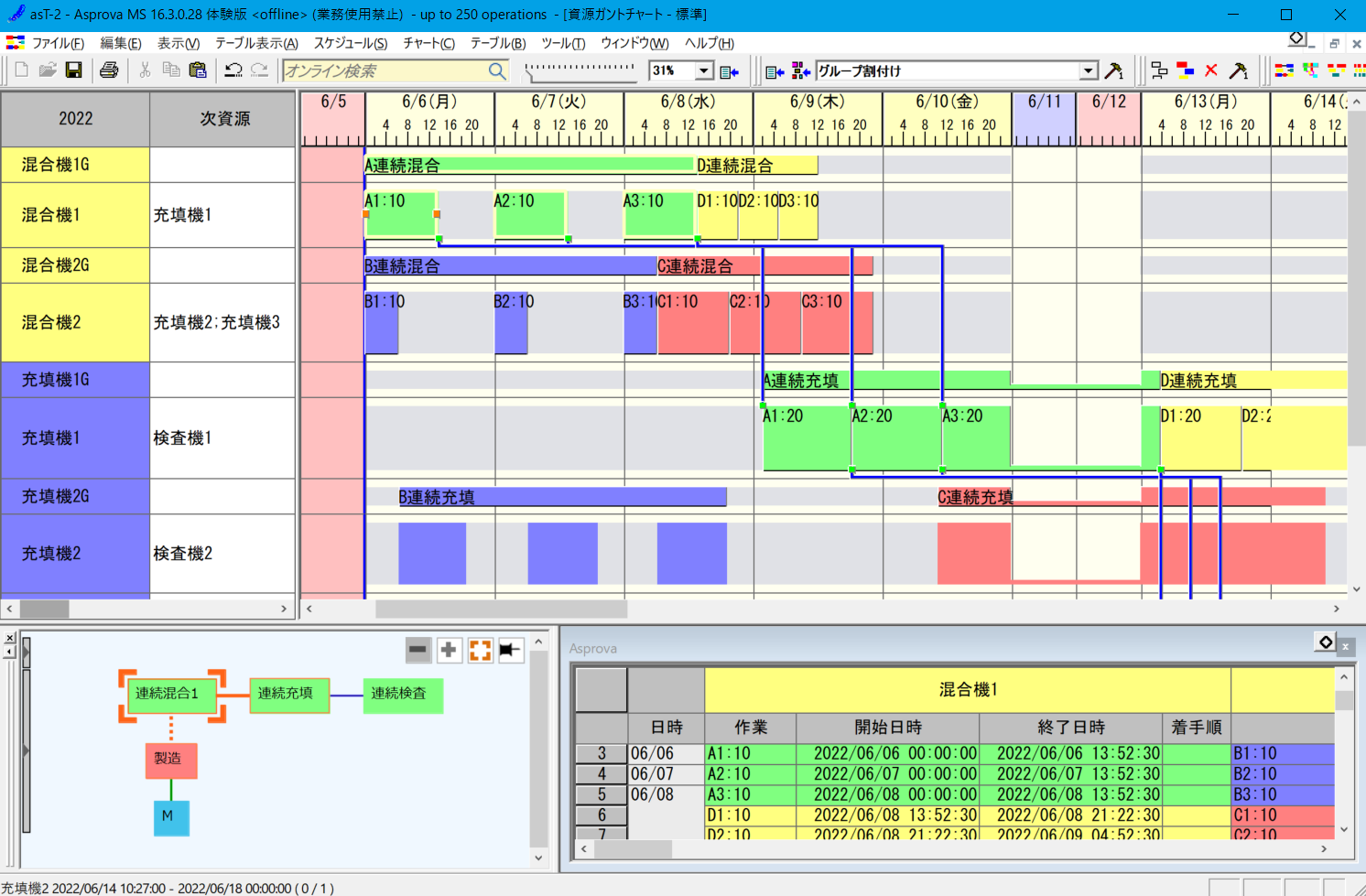
(1)生産スケジューラ導入の目的
生産スケジューラの導入を検討する製造業の多くは、日々の工場操業の中で何等かの課題を抱えています。大きく分けて計画立案業務上の課題と、製造現場の課題です。
・計画立案業務上の課題
- 1.品目点数が増えてExcelでのマニュアル作業では対応が困難。
- 2.計画の組み換えに時間がかかり過ぎる。
- 3.ベテラン計画担当者による熟練の職人芸に依存し、の標準化ができない。
・製造現場の問題
- 1.現場に中間在庫が山積みで受注オーダとの紐付きが見えない。
- 2.作業の進捗状況が見えず顧客に納期回答が出来ない
- 3.適切な作業開始日時がわからず、材料欠品によるライン停止を防ぐために、材料倉庫がモノで溢れている。
- 1.部品表(BOM)
- 品目の親子関係で階層構造を表す部品構成表。
- 2.標準作業手順
- 一つの製品を作る方法を統一した手順です。
- 3.標準時間
- スケジュールを作るにあたり、計算の元となる、作業をこなすために必要な、品目ごと、工程ごと、資源ごとの標準の作業時
- 間。現場の反発を招かないようにある程度余裕を持たせた時間を設定する必要がある。
- 4.ロット
- 受注オーダ単位または製造オーダ単位ごとの数量。
生産管理システム(ERP)は部門ごとの情報管理レベルを上げるために導入されますが、生産スケジューラは生産、物流、調達の3つの視点からの業務改善を目的としており、需要変動の中で在庫や作業員の最適化と生産設備の平準化を実現し、導入効果を定量的に評価できるソフトウェアです。
したがって生産スケジューラ導入を検討する際には、まず目標を明確にして何をもって成功とするかの評価基準を決める必要があります。
(2)Asprovaの検討から導入までの流れ
生産スケジューラAsprovaの導入を検討する場合、まず最初に無料体験版をダウンロードすることで、最大100オーダかつ最大250作業までのプロトタイプを作成することをお奨めします。
作業数とは「オーダ数x工程数」であり、受注オーダ・作業(製造指図)・在庫オーダ・購買オーダの合計となり、Asprovaをリスケジュールした後の作業テーブルの行数と同じになります。
無料体験版でもAsprovaの基本的な動作や自動スケジューリングのイメージを掴むことが出来ますが、100オーダまたは250作業という制限の中では、実際の工場で稼働する機械(ライン)数や品目数をカバーするには容量不足なので、機械数や品目数を絞って設定していきます。
無料体験版で自動スケジューリングを体感した後に、工場の実データを使った本格的なプロトタイプを作成して、実用性の面からより詳細に検討するという段階で、有料の月単位のトライアル版を使用すれば、オーダ数、作業数の制限がなくなります。1か月分~6か月分くらいの短中期の生産スケジュールをシミュレーションすることが出来ます。
生産スケジューラAsprova導入の際は、無料体験版で基本機能を確認し、有料トライアル版でプロトタイプを作成し、本番で運用可能なレベルまでブラッシュアップした後に、正式版を購入し即運用開始できるような段取りが理想です。
(3)Asprovaを動かすために必要な情報
Asprovaを動かすために必要な情報は、大きく分けてマスタ、カレンダーとシフト、オーダ・在庫の4つです。基幹システム(ERP)からExcel形式やテキストファイルでエクスポートして、そのまま、又はOLE DBからAsprovaに取り込み、リスケジュールすることで、実際に稼働中の工場の生産資源の様子をAsprova上で「見える化」することが出来ます。
マスタについては設定する条件によって多少変わってくるものの、以下の4つは最低限必要になります。
オーダはプロトタイプの対象となる計画期間分の内示・受注・出荷スケジュールなど、在庫は必要に応じて棚卸在庫情報と、発行済未入荷の原材料の発注書情報を登録します。
(4)生産スケジューラ導入は業務改革とセットが基本
プロトタイプの評価後に正式ライセンスにて導入プロジェクトが開始されますが、一般的には基幹システムとの連携や外部からのデータ取込みのためのインターフェイスの開発や、出力帳票や現場モニター表示用画面のための追加プログラムなど、既存業務と連携するための補修材としてのプログラム開発が発生します。 しかし既存業務を残すためだけの周辺プログラムの開発は、システムを冗長化させ、何よりも生産スケジューラ導入の目的が既存業務のシステムへの置き換えというように、導入意義が矮小化されてしまうため、既存業務のアップデートを前提としたものであるべきです。 業務改善を考える場合の定番であるECRS(イクルス)の原則である排除(Eliminate)、統合(Combine)、交換(Rearrange)、簡素化(Simplify)の4つの考え方に基づき、あくまでも最小の作業負荷で最大の成果が出るように業務の流れを再構築し、標準業務フローSOP(Standard Operation Procedure)を作成します。 そして業務の流れが変われば、必ずデータの流れや構造も変える必要が出てきますので、生産スケジューラに取り込む情報も、既存の基幹システムからの情報だけでは不十分である可能性があり、これを機にデータの見直しやExcel管理されていたデータのマスタ化などを行う必要があります。