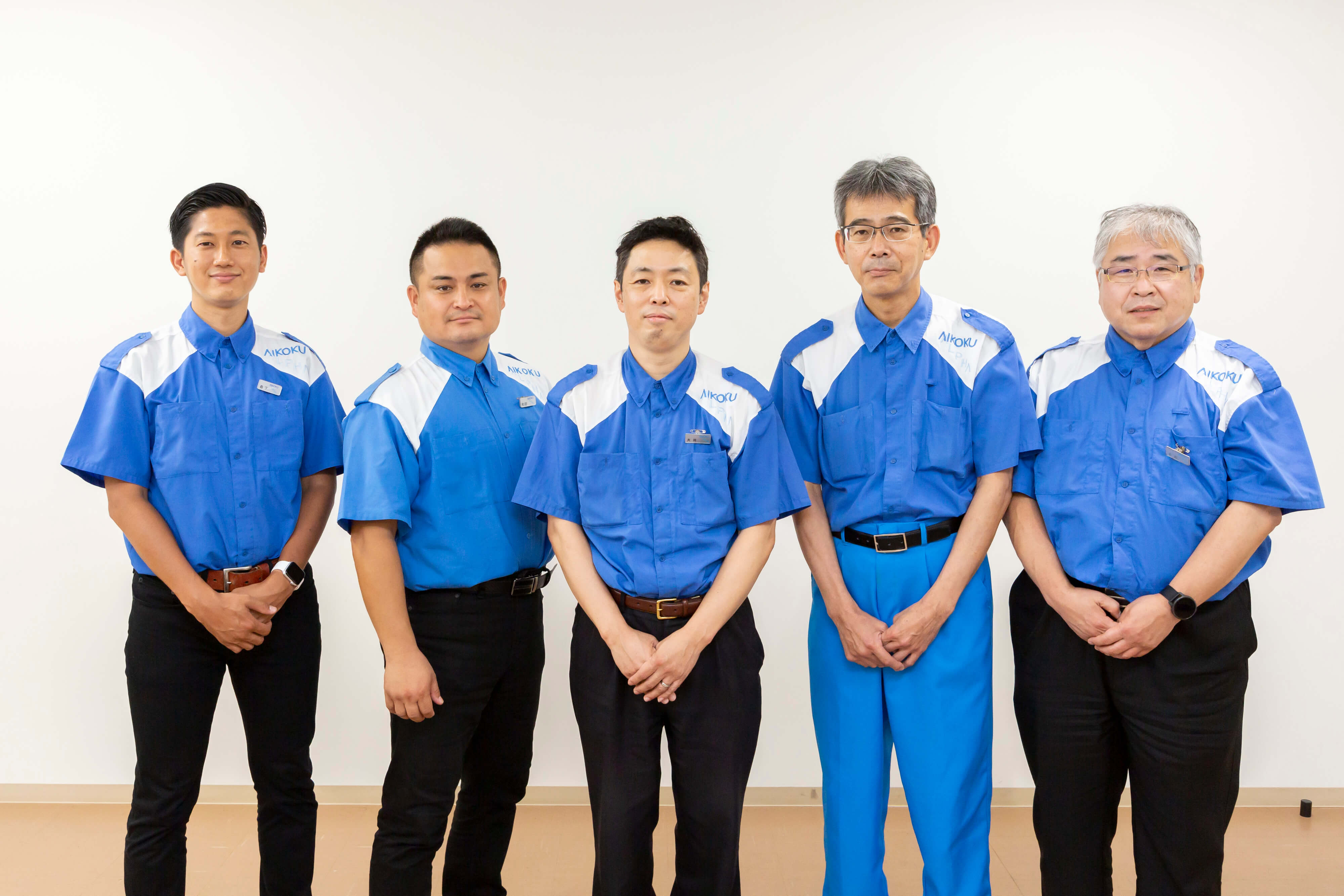 |
持続可能性を考え、生産スケジューラをAsprovaにリプレース。
ミスを減らして、担当者のプレッシャーを軽減し、計画工数を40%削減。 |
精密冷間鍛造で高い技術力を持つアイコクアルファ株式会社CF事業部(以下、アイコクアルファ)では、時代遅れになった生産スケジューラをどうリプレースするかに頭を痛めていました。26年前に導入した生産スケジューラの開発会社が倒産してしまい、サポートが受けられなくなり、遅い処理速度、システム障害などにより生産計画立案に支障が生じていました。
この状況を打開すべく新しい生産スケジューラを探し始めましたが、どれも一長一短で決めかねていたところに出会ったのが「Asprova APS」(以下、Asprova)です。Asprova導入により、旧生産スケジューラのリプレースと効率の良い生産計画立案を可能にした経緯についてアイコクアルファ株式会社CF事業部 FDCTシニアマネージャー(生産計画・購買) 大井実氏、CF事業部 FDCT FPCG 和田昇氏、CF事業部 FPCG 森下権太氏の3名と、導入をサポートされたトーテックアメニティ株式会社(以下、トーテック)松野隼弥氏に伺いました。
|
■アイコクアルファ株式会社 本社工場
■住所:愛知県稲沢市祖父江町森上本郷十一、4番地1
■設立:1943年8月
■資本金:12億円
■従業員数:1,040人(2020年8月現在)
■事業内容:精密冷間鍛造、ハンドクレーン、精密切削加工、CAD/CAMシステム開発・販売
アイコクアルファ株式会社のサイトはこちら
|
アイコクアルファでは、精密冷間鍛造により等速ジョイント内輪のトラック溝やクラウニング付きサンギヤの歯面などを高い精度で製造しています。
-- 精密冷間鍛造の工程と課題について教えてください。
冷間鍛造とは、材料の金属に熱を加えず、常温のまま圧力を加えて、金属を変形させながら成形する加工方法です。温間鍛造などに比べると常温で加工するので寸法精度が高く、材料を削らないのでムダが出ません。弊社では、工程設計や金型設計、金型製作について長年積み上げた独自のノウハウを活用して精密冷間鍛造を可能にしています。また、切断、焼鈍、ボンデ、冷間鍛造、切削、浸炭焼き入れの工程を一貫して行うことで、トラック溝やギヤ歯面を鍛造肌のままで研磨なしでも使えるような高精度化を実現しています。
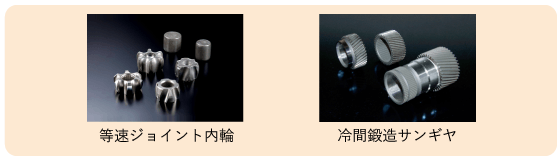
冷間鍛造製品
|
-- 生産計画を立てる際の課題について教えてください。 |
弊社では、26年前に生産スケジューラと鋼材仕入、棚卸などを行うシステムを導入しました。以来、このシステムをインフラとして使って生産計画を立ててきましたが、さすがに古さが目立つようになってきました。システム導入以来、生産量は約1.5倍までに増えているのですが、旧生産スケジューラは処理速度が遅く、エラーが出るようになりました。また、システム障害が発生し、2~3日復旧できないこともありましたが、サポートを受けようとしても、開発メーカーが倒産しており、サポートが受けられません。
古い状態のまま使い続けていたので、条件を入力し、生産計画を出力するだけで精いっぱいとなってしまい、生産計画のミスを現場から指摘されたり、数量不足を急いで挽回してもらうようなことが続いていました。旧生産スケジューラにはエラー表示機能がなかったので、計画担当者がミスを探し出していたため、計画立案に60時間かかっていました。納期遅れを出さないために生産計画のミスをゼロにするプレッシャーは相当なものがありましたし、他の人には引継ぐことができない仕事になっていました。効率的な生産計画を立てるような余裕もありません。このように、旧生産スケジューラの不具合が目立つようになったことがAsprovaを導入するきっかけとなりました。 |
旧生産スケジューラでの生産計画立案
|
-- どのようにAsprovaを導入されたかを教えてください。 |
「旧生産スケジューラの不具合と計画担当者のプレッシャーがなくなりました」(大井氏) |
持続可能性がないとは言え、旧生産スケジューラを重要なインフラとして使っていたので、その機能は継承したい。その上で新しい、便利な機能を追加したい。そう考えて、新しい生産スケジューラを探し始めました。 ところが、難題が見つかりまして、旧生産スケジューラの機能を継承するには独自言語で書いてあるロジックを解読した上で、新生産スケジューラに移植しなければならないことがわかりました。 もともとの開発メーカーが倒産してしまったので、旧生産スケジューラの解読、新生産スケジューラへの移植と導入、導入後のサポートと、リプレースに伴う高いハードルをなんとかクリアできないかと思っていたところ、大阪の展示会でトーテックさんからAsprovaの説明を聞き、これだ!と思いました。 |
AsprovaはシェアNo.1で、会社の規模も大きく、今後も継続してサポートが受けられるという点で安心できました。また、パソコンが苦手な人でも使える点にも惹かれました。他の製品も検討しましたが、生産を止めることのない、新しい生産計画のしくみ作りとサイバー攻撃などを受けた際の迅速な復旧も考えると、不安がありました。 さっそく、トーテックさんとAsprovaへの移植・導入、運用サポートなどについて相談したところ、「やります」と心強いお返事をいただけたので、Asprovaへのリプレースを決めました。 導入が決まってからは、弊社のシステム部門と生産計画部門で連携して、トーテックさんと二人三脚で進めました。旧生産スケジューラで行っている処理を説明するのがむずかしく、もどかしかったのですが、うまくサポートしていただき、移植作業はスムーズに進みました。 |
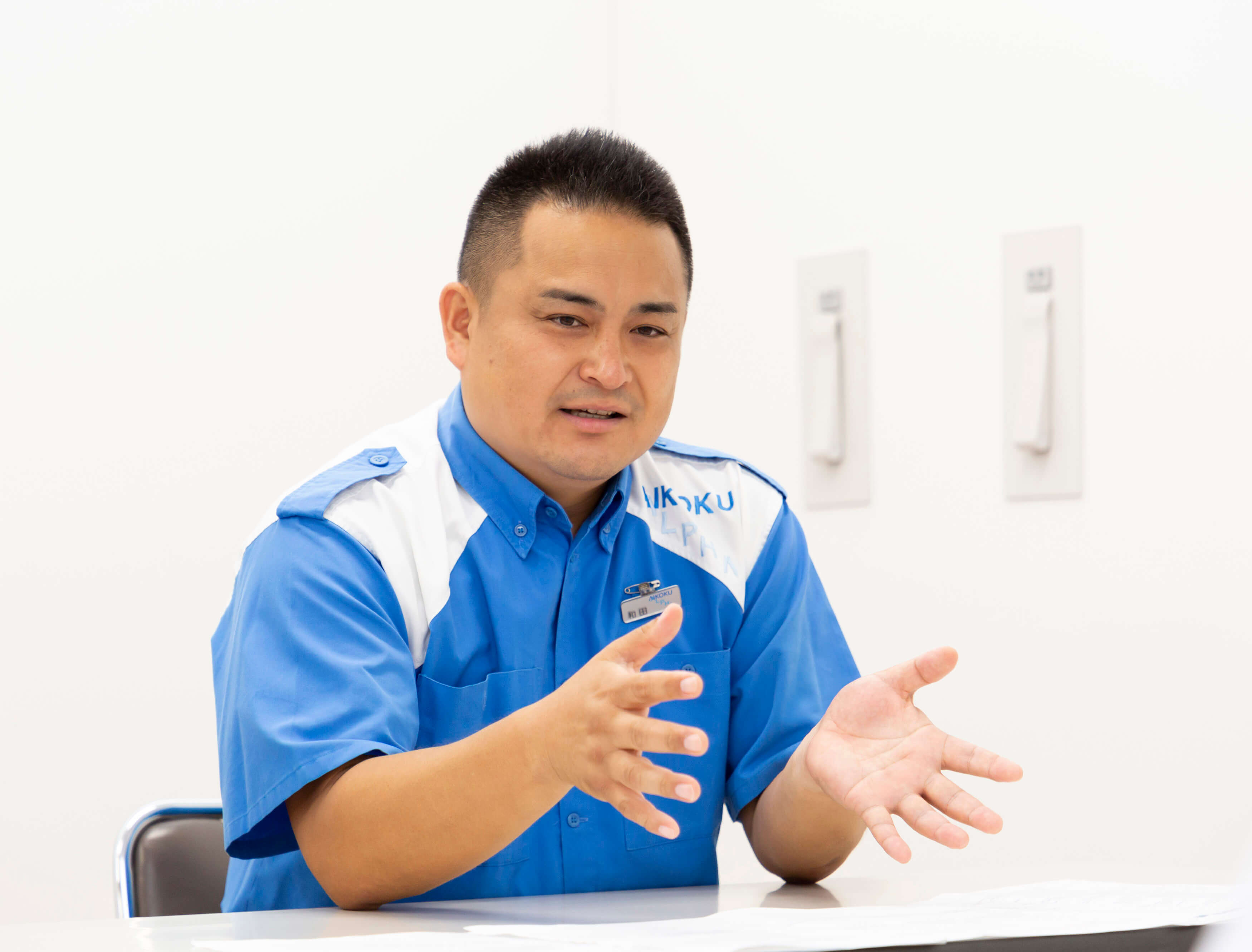
「計画立案が早くなり、ミスが減ったので、生産の効率化などを考える余裕ができました」(和田氏) |
生産計画を担当する和田氏は、Asprovaにリプレースした効果を次のように語っています。 「弊社では、国内向け製品の管理コストを抑えるために在庫をほとんど持っていません。その一方で納期遅れはゼロにしなければならないという厳しいビジネスになっています。製品在庫を持たずに納期遅れをゼロにするために、生産計画を綿密にチェックして納期遅れにつながるミスをゼロにしなければならないという要求がありました。 旧生産スケジューラでは、生産計画の計算に4~8時間かかる上に、さらに手作業の修正が必要でした。そうしないと、使える生産計画にならないからです。また、生産計画に矛盾があってもアラームが出ないので、これも手作業で修正していました。こういった作業の負荷が計画担当者に集中し、大変なプレッシャーがありました。 Asprovaを導入してからは、計画に不備があればアラームが出ますし、計画担当者の頭にあったノウハウをシステム化できたので、バラつきの少なく、精度の高い生産計画が作れるようになり、残業も減りました」 |
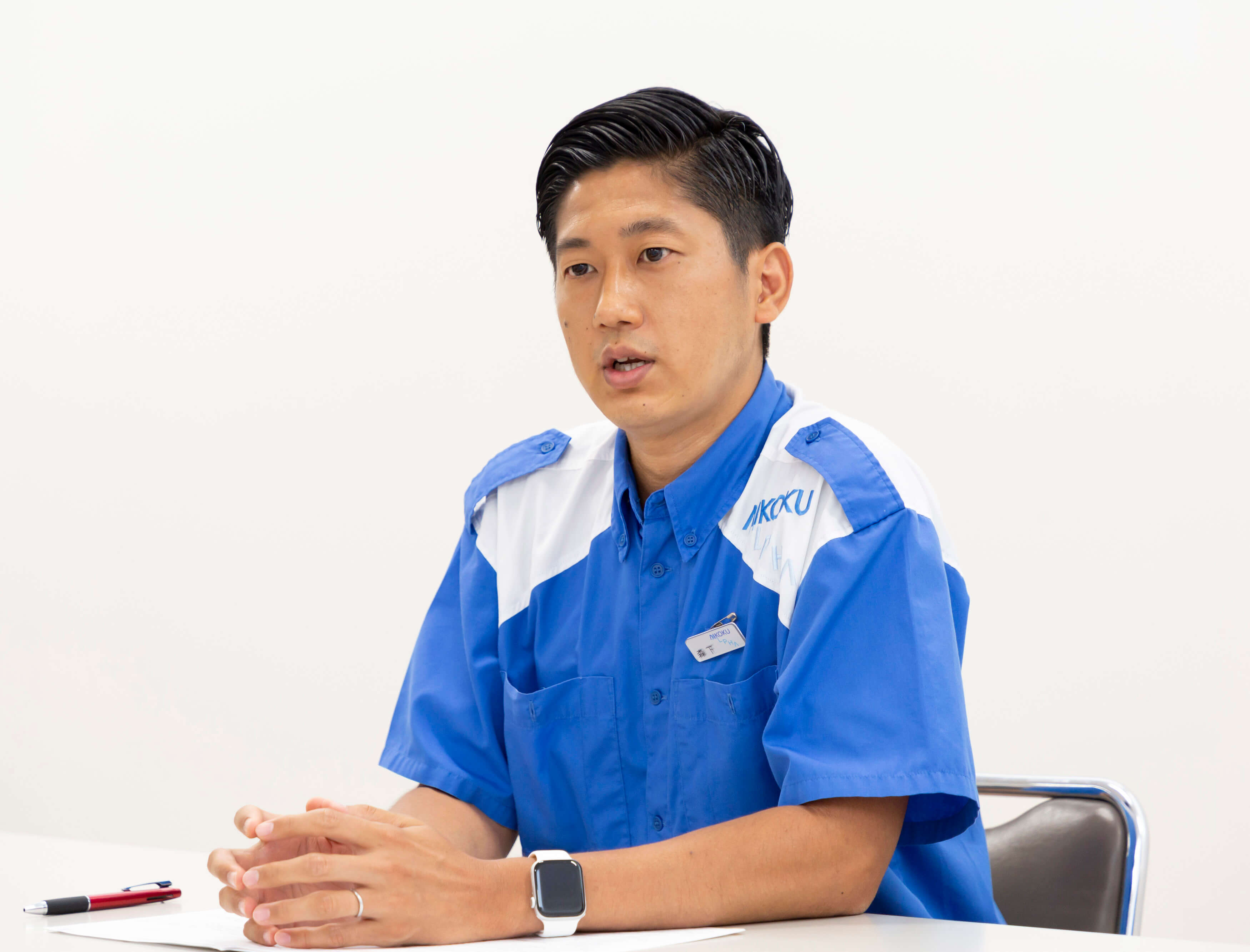
「旧生産スケジューラでは独自言語で機能が記述されていたので、解読に苦労しました」(森下氏) |
システム担当の森下氏は、トーテックと協力して導入を進めたことが成功の要因だと語っています。 「計画担当者の要望をトーテックさんにつなぐのが私の役割でした。単純に旧生産スケジューラの機能を移植するのではなく、トーテックさんと相談しながら、現場の要望を実現したのが良かったと思います」 |
-- トーテックアメニティ 松野隼弥氏のコメント |
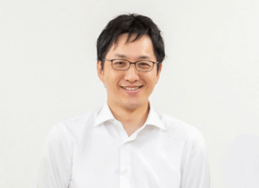
導入を担当された、トーテックアメニティ株式会社 産業システム事業部 第1システム部 松野隼弥氏
|
旧生産スケジューラをAsprovaにリプレースしたいというお話をいただきましたが、旧生産スケジューラでは独自言語で機能が記述されているので、まずその解読を弊社内の他部署で行って、どのように機能を実現しているかを理解した上でAsprovaに移植しました。また、旧生産スケジューラでは実現できなかった機能についてもご要望をいただき、Asprovaの強みを生かした形で提案しています。
旧生産スケジューラは内部処理のしくみがわからないためアップグレードもままなりませんでしたが、Asprovaを導入することで新しい機能の提案もできますし、将来に向けても継続的にサポート・機能強化ができますので、安心してお使いいただけます。
|
-- Asprovaを導入した効果について教えてください。 |
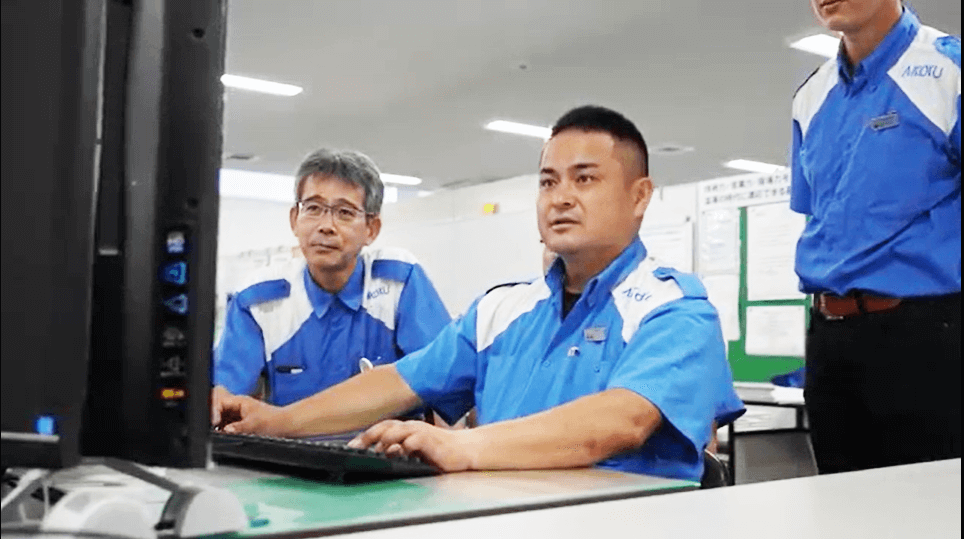 |
大きく分けて、二つの効果があると思います。一つは時代遅れになった旧生産スケジューラを最新のAsprovaにリプレースしたこと。もう一つは、将来に向けて継続的にサポートが得られるようになったことです。 |
最新のAsprovaにリプレースしたため、旧生産スケジューラで困っていたシステム障害やエラーなどがなくなり、スムーズに生産計画が立案できるようになりました。以前は6日間60時間かけて生産計画を立てていましたが、4日間36時間まで40%削減できました。また、矛盾のある生産計画にはアラートが出たり、納期遅れにはエラーが表示されるので、生産計画のミスがなくなりました。 納期遅れを出さないため、ミスのない生産計画を立てなければというプレッシャーも軽減され、これまでは余裕がなくてできなかった電力削減や工場全体に関わる施策などにも取り組めるようになりました。 旧生産スケジューラは、開発会社が倒産してしまったので、機能や処理速度に不満があっても改善できませんでしたし、障害が起きると、弊社内のMS事業部の技術者も駆り出すなど、総動員で回復しなければなりませんでした。Asprovaを選択し、トーテックさんにサポートしていただけるので、将来的に継続して使えるようになりました。
|
-- アスプローバ社への要望や期待があれば、教えてください。 |
Asprovaにリプレースして、生産計画を立てる工数は40%削減できました。良い成果なのですが、まだ60%残っているとも言えます。今後もできるだけシステム化を進めたいと思っています。
例えばですが、精密冷間鍛造の精度を上げるためには、段取り作業でさまざまな条件を少しずつ変えて、最適な加工条件を見つける必要があります。この作業は微妙な調整、検査、再調整の繰り返しがあり、熟練作業者のカンやコツに頼っているため生産計画も手作業で行っていますが、いずれは自動化したいですね。
Asprovaを導入し、順調に稼働しているので、さらに上を目指したい、改善したいという気持ちがあります。現場の声、私たちユーザーと共に成長できるようにしていただけるとありがたく思います。
|
-- Asprovaの導入を検討されている方にアドバイスがありましたら、お聞かせください。 |
Asprovaのシェアが高いということは、その価値が市場で認められているという証拠です。弊社では、旧生産スケジューラが古くなってしまったことがきっかけでしたが、生産計画に悩みを抱えている方は、思い切って導入してみると今までと全く違った景色が見えるので、トライしてみることをおすすめします。サポートもしっかりしていますし、ベンダーさんも相談や要望に応じてくれますので、安心して任せられます。
|
次フェーズに続く>>>
Solverオプションによる更なる効率化
* 取材日:2022年7月6日
* 記載の担当部署は、取材時の組織名です。
|