MRP glossary TOP > The functional roles an MRP production control system performs > Engineering Data Control
Engineering Data Control
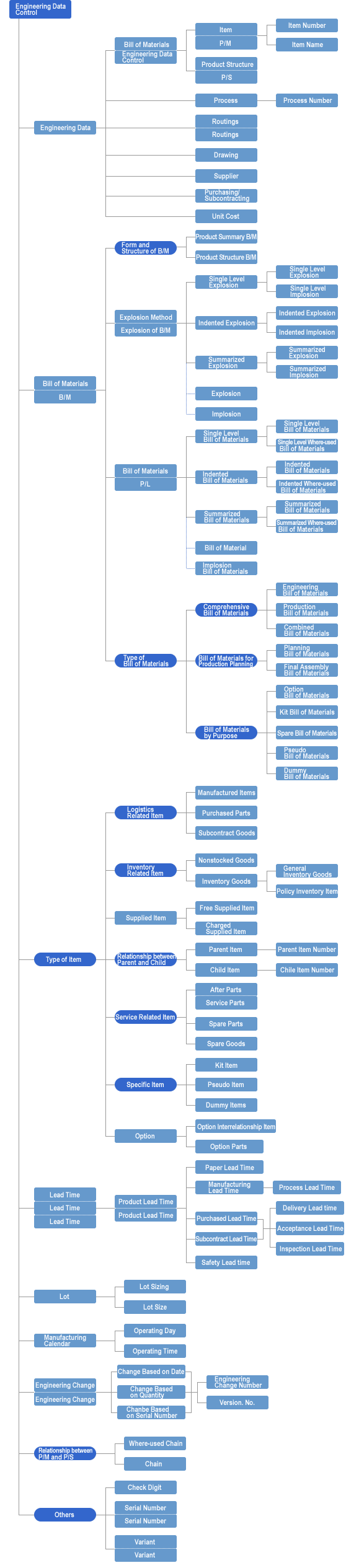
- Work descriptions:
-
An wide variety of information is used to produce products. For example, a B/M (Bill of Materials) is necessary to explore assemblies, parts, materials, etc. used as a component of the product, or an item is used to fix the delivery or logistics date. The technical information called a process or routing is also needed to check the process for producing assemblies and parts and the production routine. In this way, the information which are necessary for production control, and can be a base of planning and governing works is called engineering data.
Previously, no division has controlled and maintained the engineering data in an integrated manner, and only necessary engineering data has been recorded in a ledger by each division such as purchasing or manufacturing. The division to centrally control and maintain the engineering data is vital in order to implement the production control system using computer programs. In addition, most divisions in a factory, including engineering, producing technology, administration, purchasing, manufacturing, and subcontracting, are involved in generating the engineering data. - Problems:
-
Possible problems in the engineering data control system are as follows:
1. It takes long time to prepare a B/M for new products, and the process has manual and computer-aided processing, causing the site confusing.
2. New products are being collected at a time, and thus necessary items are not prepared in a B/M.
3. The diversification of a product and ephemeralization of its life cycle make the timely update of B/M difficult.
4. The engineering specifications are too frequently changed, and have not been managed, making the site and subcontractors confusing.
5. Since the division deals with too much data, it takes much time and cost to control and maintain it.
6. Since each person in charge belonging to various divisions creates the engineering data, there are cases where necessary information is missing, wrong, and inconsistent with other information.
7. The data lacks credibility because it is difficult to centralize the data, and its changes are not been rapidly reflected on it. - Functions:
- The conventional distributed management system causes duplication of data, and thus its promptness and credibility are still problematic if any changes are to be made. In order to aim for more advanced production control system by using more timely and high-quality engineering data, DB/DC (Database/Data Communication) technology using computer programs is indispensable for its implementation. The engineering data control system generates, manages, and queries the engineering data necessary for production by fully utilizing the DB/DC technology. The engineering data includes such information as drawings, process flows, processes, routings, facilities, product loads, and subcontractors. The system deletes, adds, and update such huge engineering data in an integrated manner. In addition, the engineering data is categorized into several standard values: physical unit, lot size, lead time, standard capacity, maximum capacity, and safety inventory. These values (set initially) are required to be always updated in response to changes, if any. How rapidly and flexibly the B/M is controlled and maintained in response to the frequently-made changes in engineering is very important. In order to implement such control and maintenance, it is critical to regularize the engineering change procedure and rapidly grasp the influence of the engineering changes.
- Tips for MRP
- According to the survey conducted by a computer manufacturer, the most computerized function is inventory control (51%) and the least computerized one is demand forecast (2.1%) among various functions of production control system. It also shows the functions which will be the most computerized in the future are MRP or material requirements planning (44.7%) and cost control (42.6%) in descending order of computerization, while quality control (10.6%) will be less computerized. Regarding future noncomputerization, quality control (85.1%) takes first place, as expected, following demand forecast (80.9%). On the other hand, such functions as receiving/inspection control, inventory control, purchasing plan, cost control, and material plan are seen to be more and more computerized.
Reference:JIT Business Research Mr. Hirano Hiroyuki
Inventory Control | The functional roles an MRP production control system performs | Purchasing Planning and Acceptance/Acceptance Inspection Control